Class-A surface • Finite Element Analysis • Topology Optimization • Photorealistic Rendering
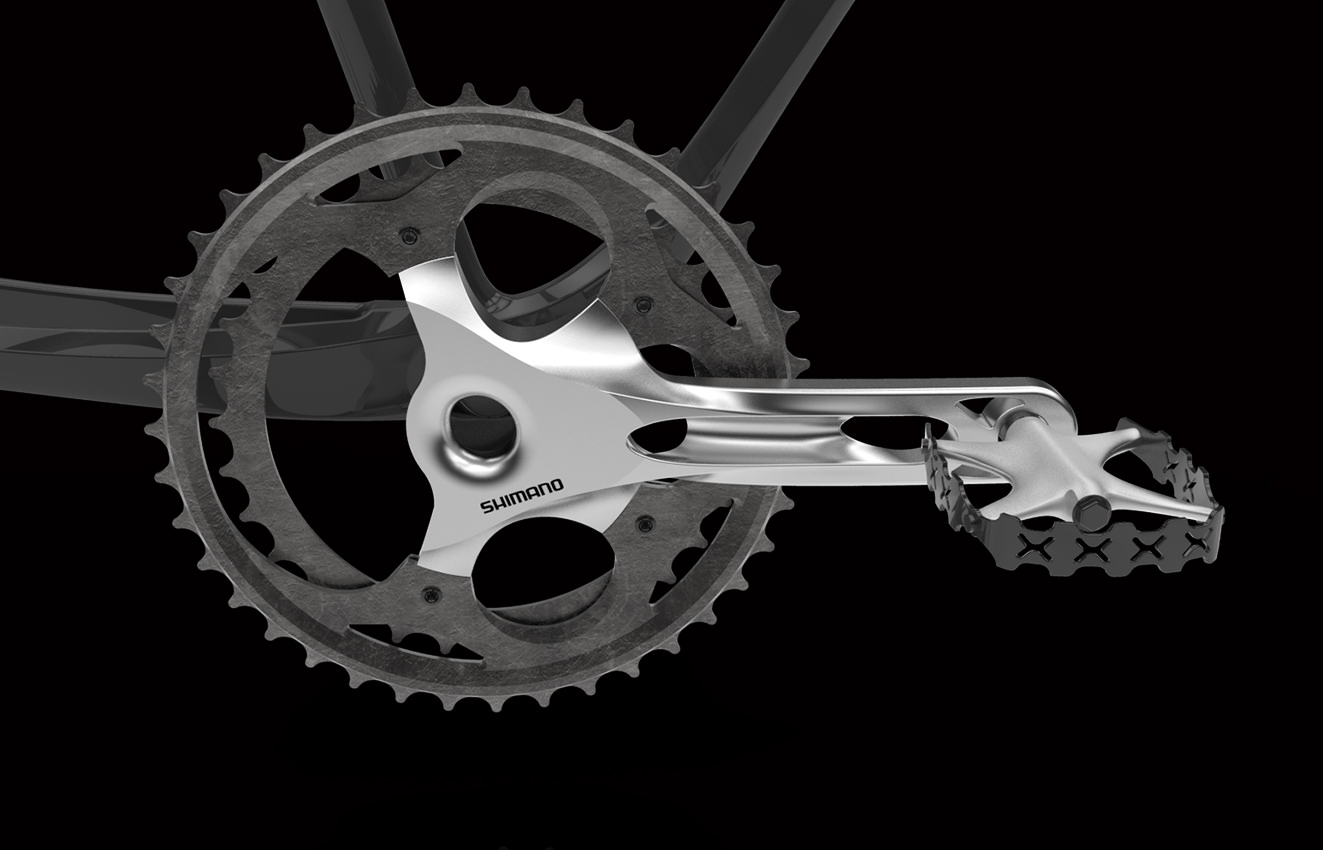
Objectives
With the objective of making the lightest crankset possible. I chose to design a 6061-aluminum 3D-printed crank arm. First, I needed to understand the forces at play. With 270 lb total on a 10% grade, you have 27 lb of tangent force on the tire. With a 26" tire, that's about 702 inch-pound of torque. With a gear ratio of 4:3, you need 702 * 4/3 = 936 inch-pound of torque on the crank. With a 6" crank, that's 156 lb average force.
The force on the pedal varies with the angle of the crank. When the force is vertical and the crank is horizontal, you get the maximum torque from a constant force. The torque is then equal to the force times the crank length. Longer legs do better with longer cranks. A longer crank requires less force on the pedals. If the crank is too long, your bottom pedal may drag on the ground when you lean in a fast turn.
Surfacing design
PTC Pro Engineer • 3D scanning • NURBS surfacing
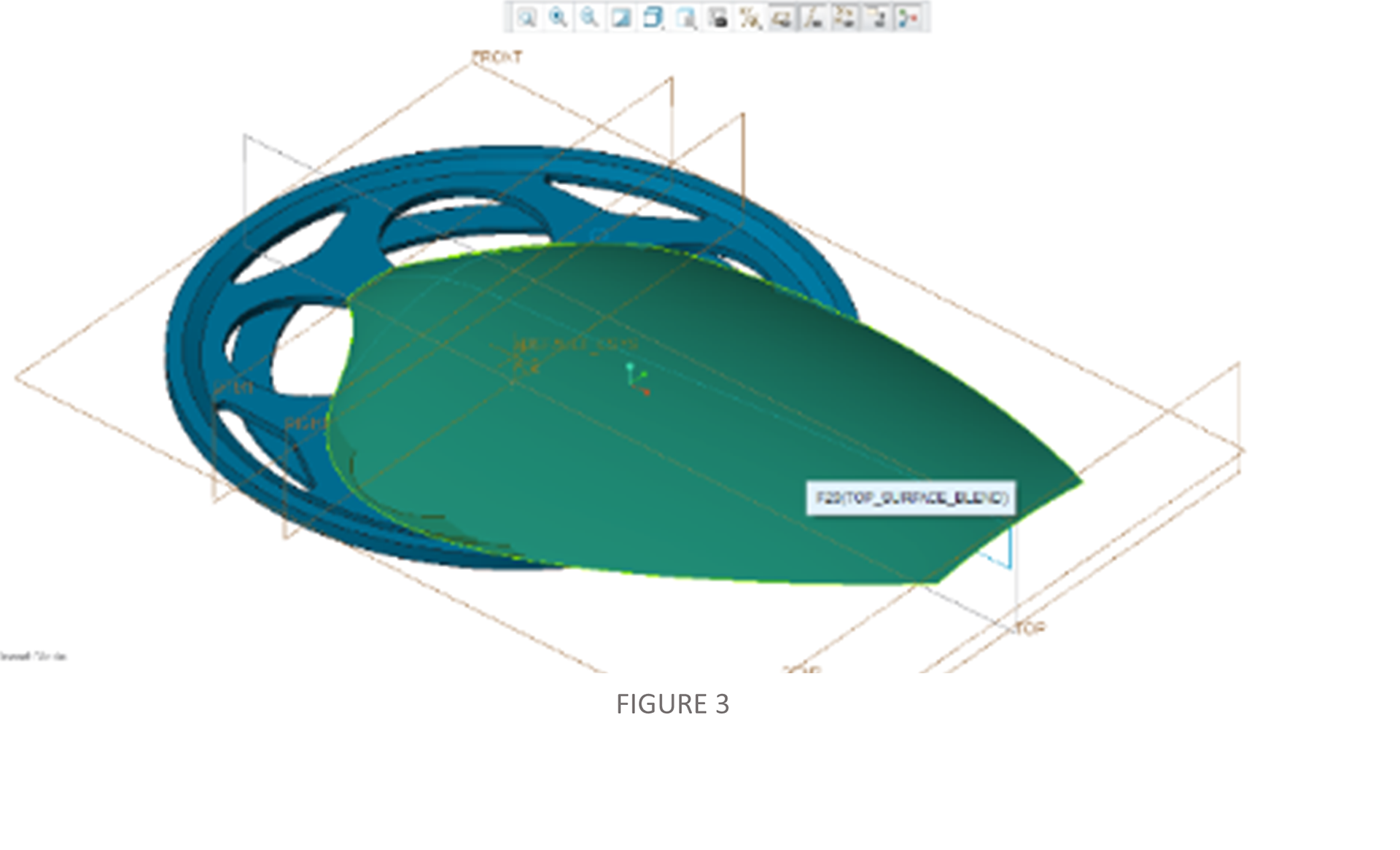
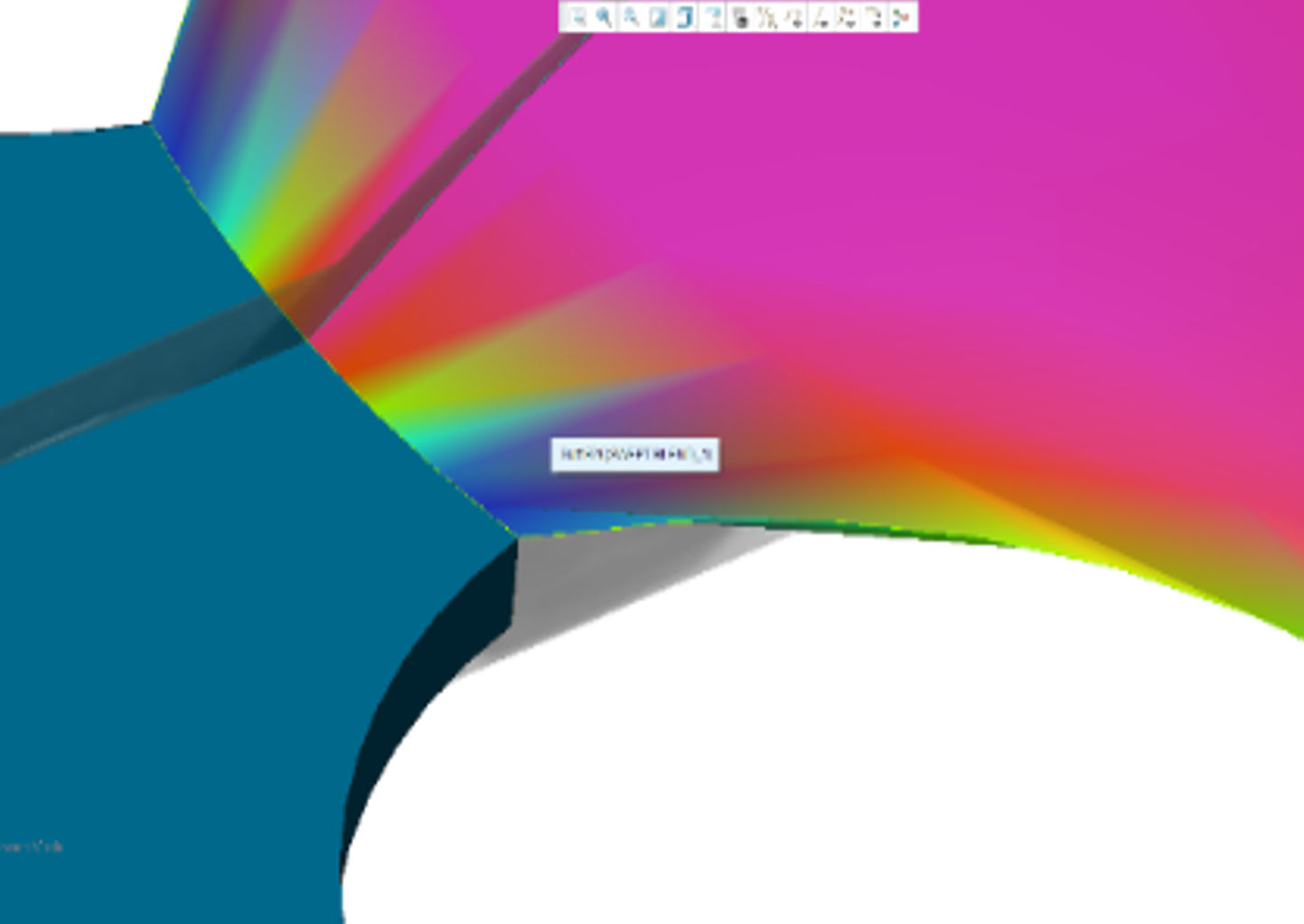
Surface pinch, to trim
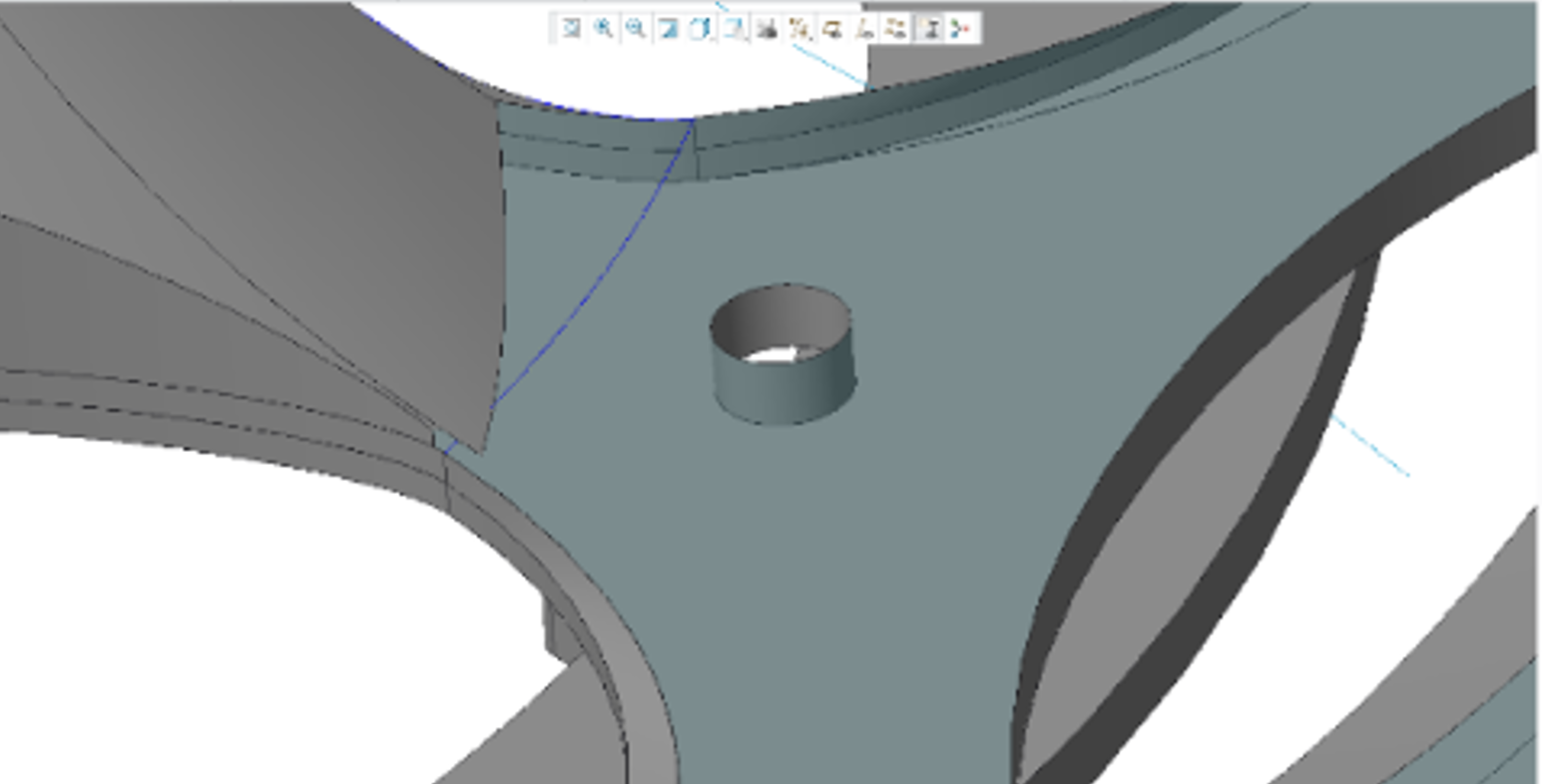
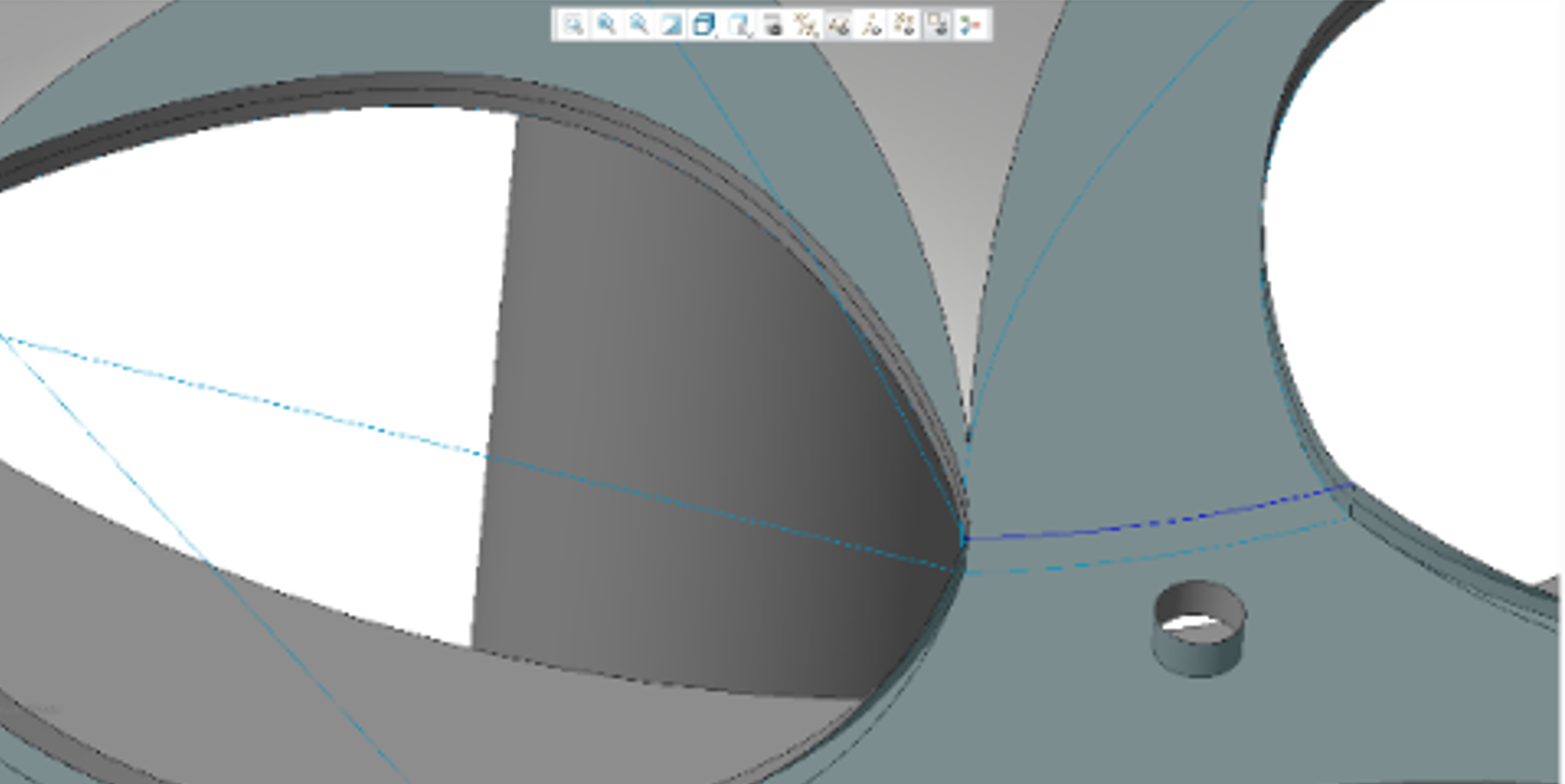
3-sided surface issue
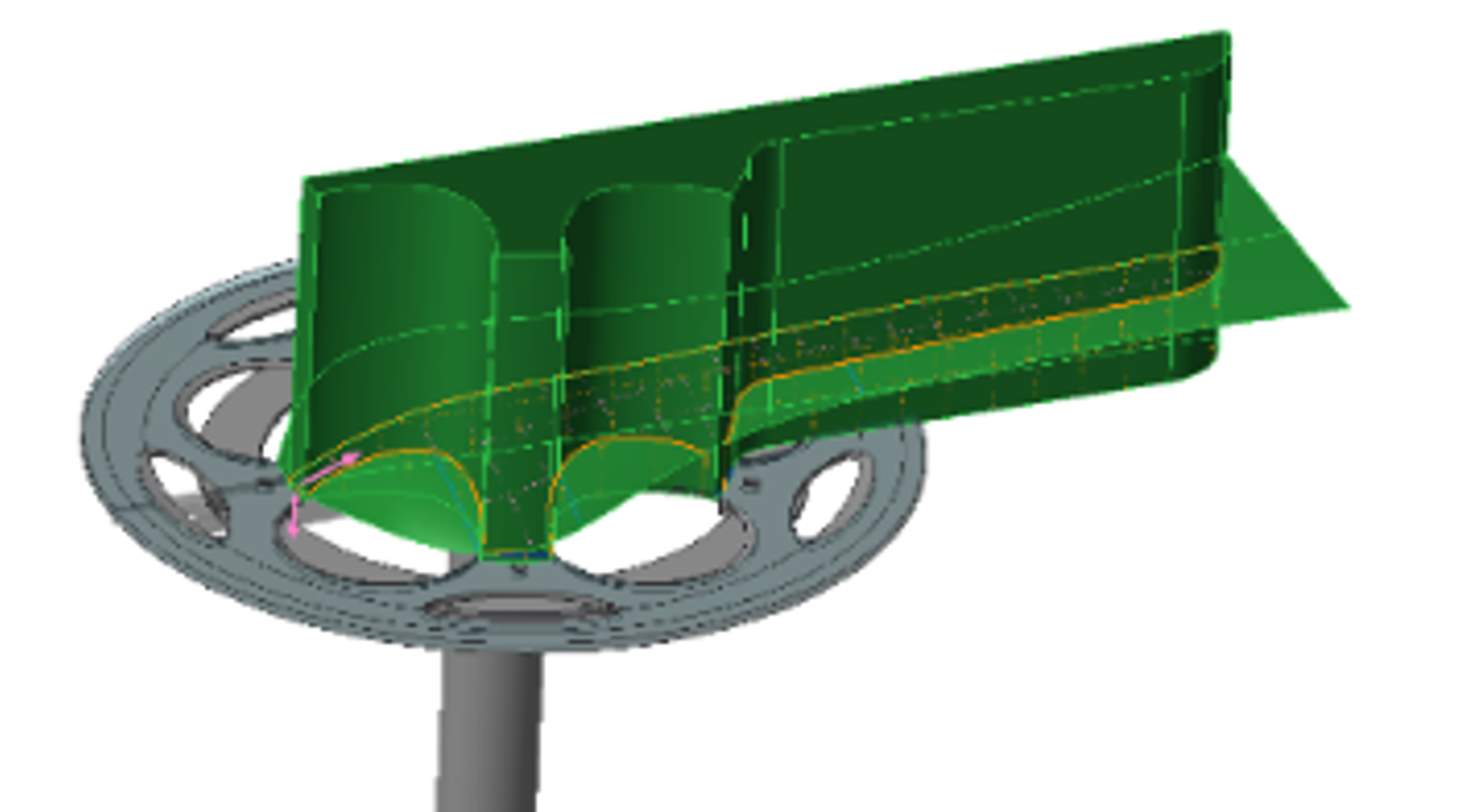
Overbuilt construction
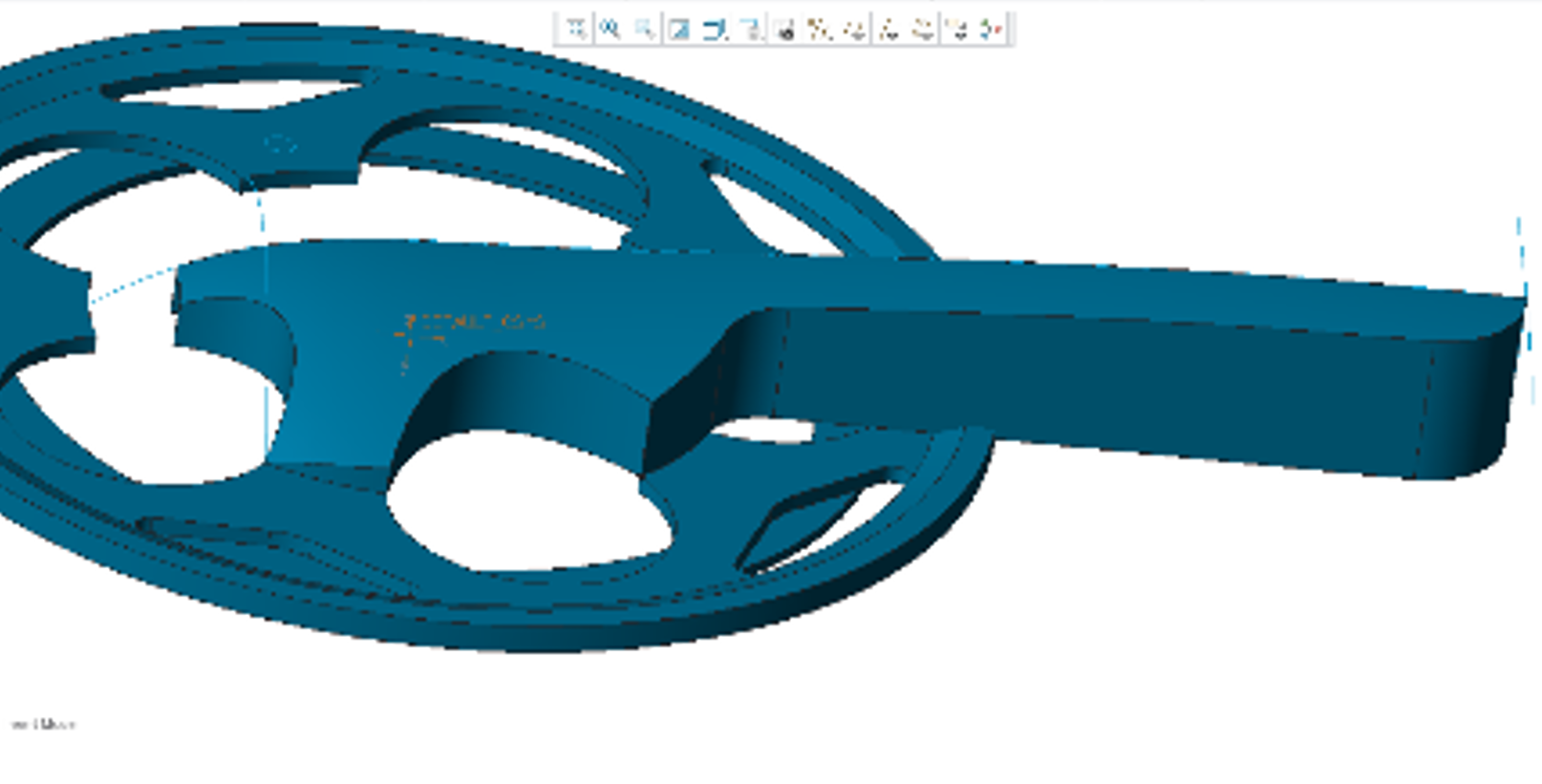
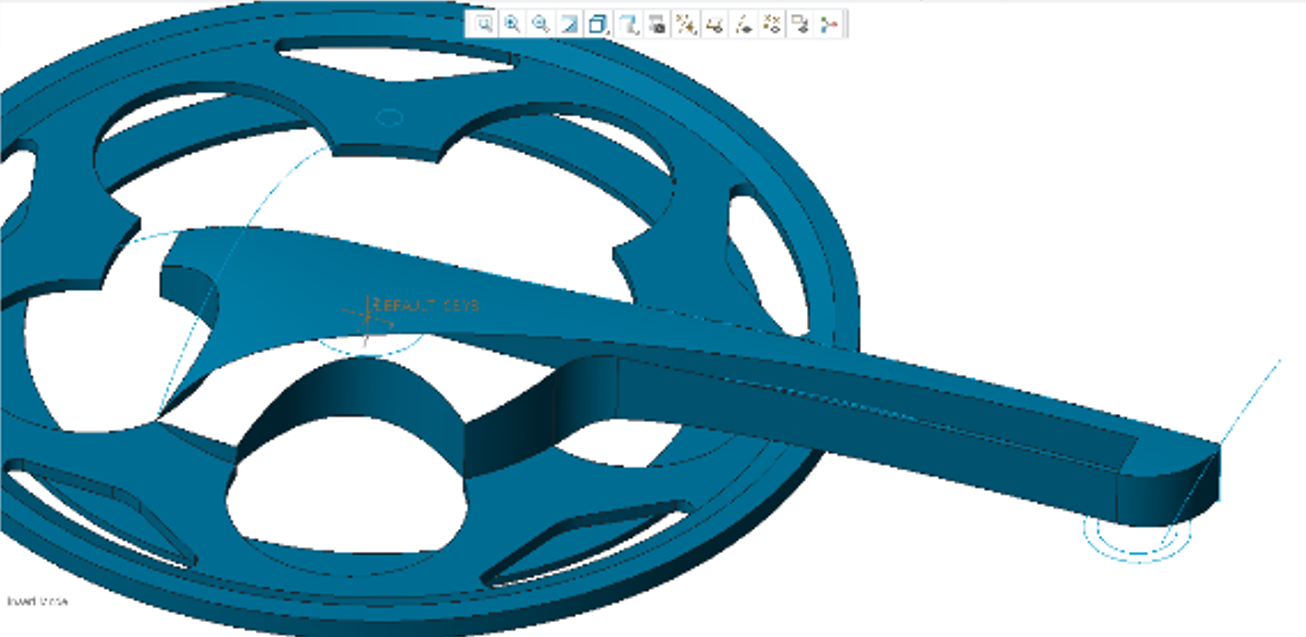
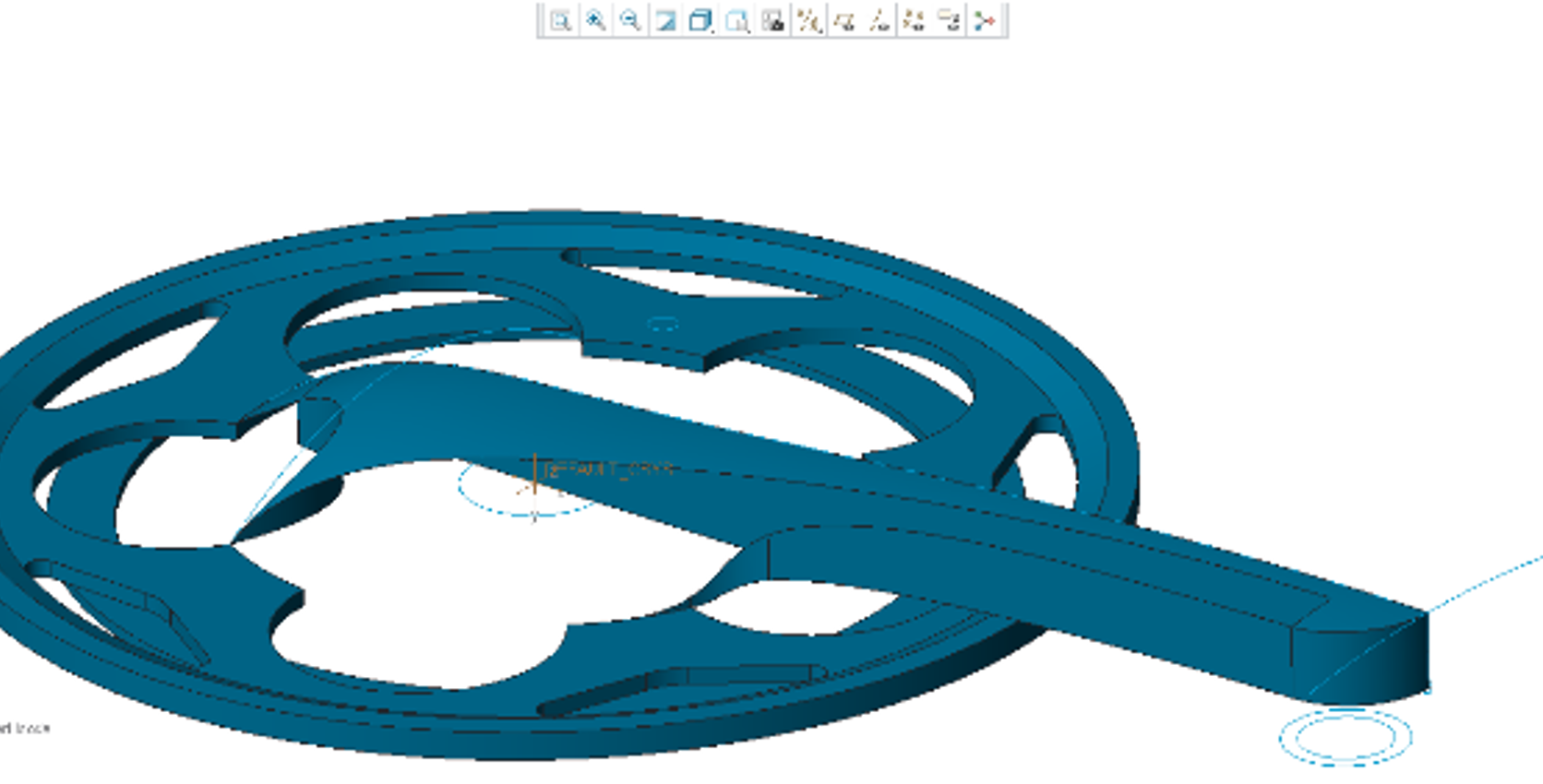
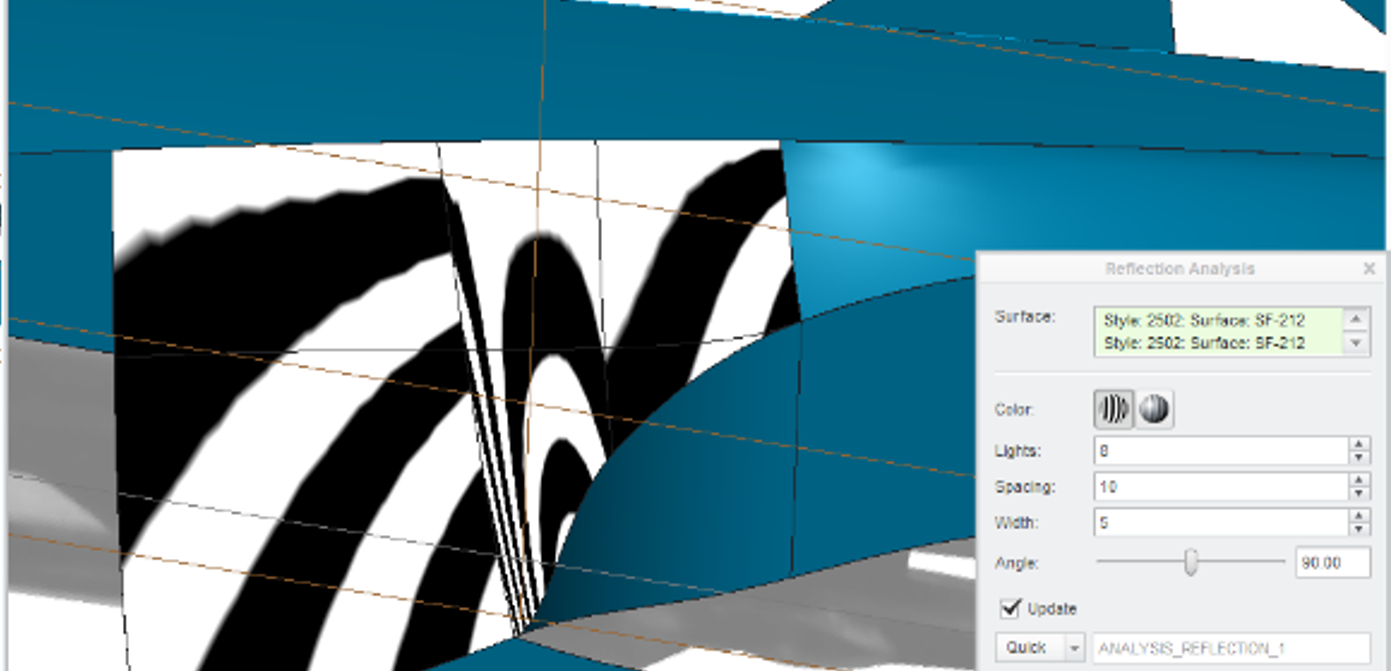
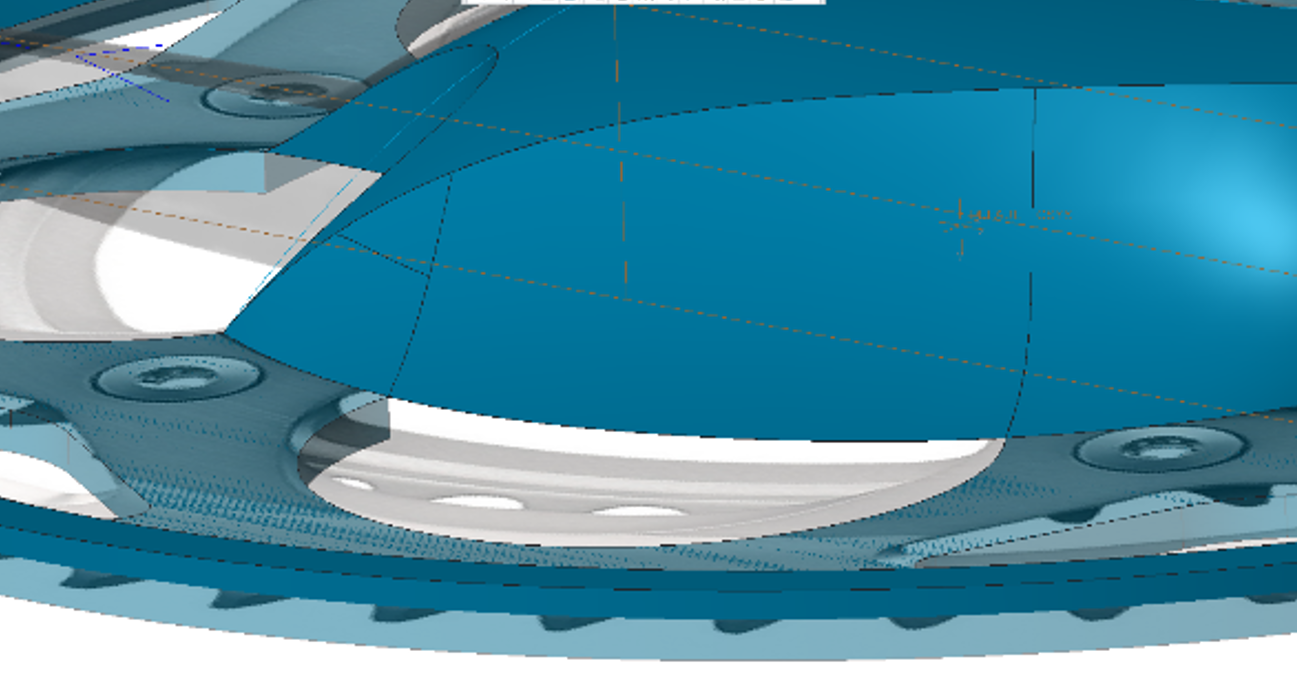
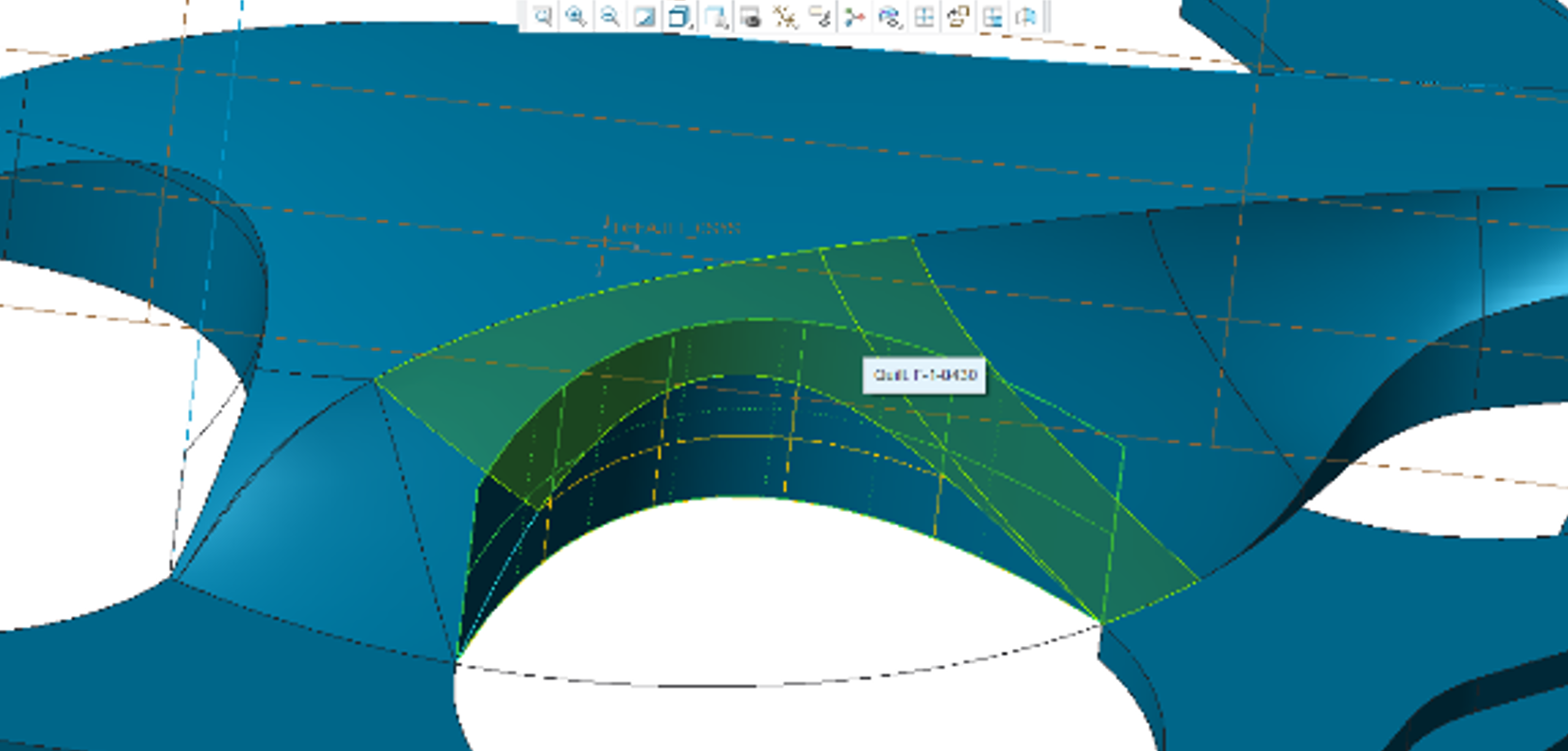
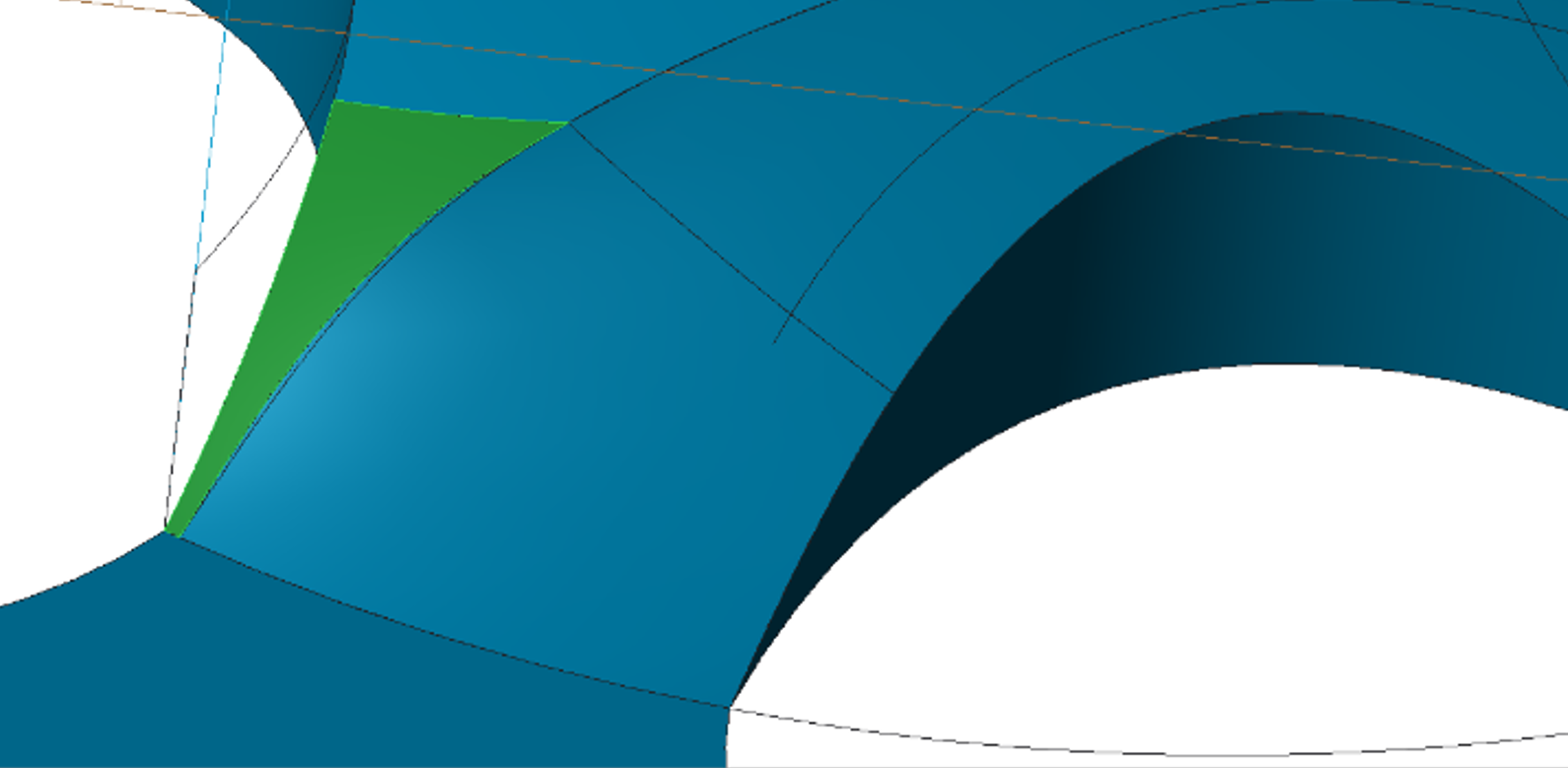
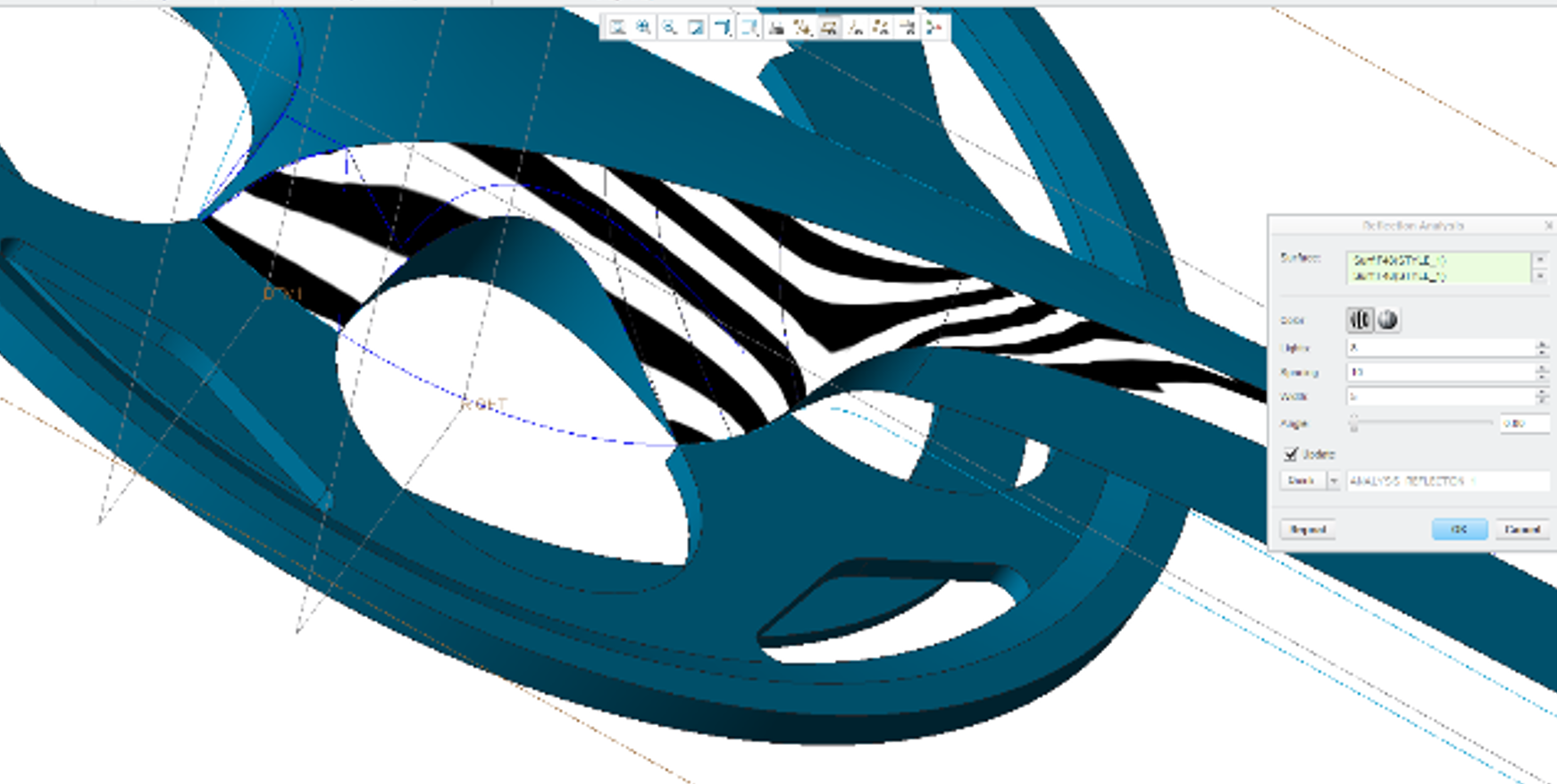
Topological Optimization
Autodesk Inspire • Rhino 6
After achieving a class-a surface on the crank that matches Shimano's crankset, I set about systematically reducing the weight using an engineering method called topological optimization. This can help me to gain insights about where the load is being applied. I used Finite Element Analysis to see where the stress concentrations and maximum deflections are then built in a factor-of-safety into the optimizer and generated multiple 3D meshes based on the generated output. I repeated this process at different angles.
The optimizer came up with some novel solutions, removing the rear support and removing material away from the crank axle center removed a lot of weight. I could have applied process constraints at this point, but this was a perfect match to remove as much weight as possible using 3D printing.
I then built a new model that took the insights from the optimization and used FEA to validate the shape.
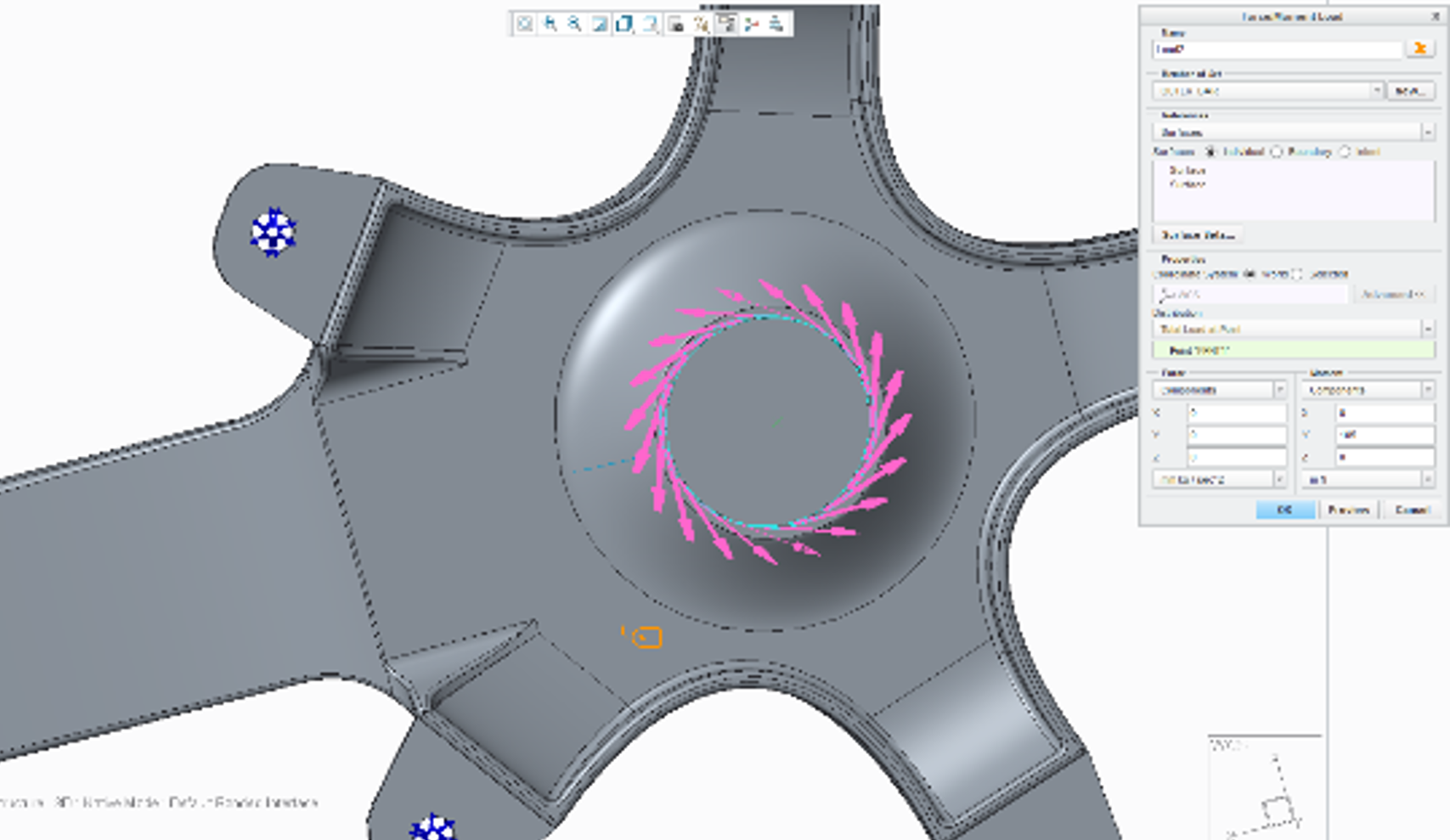
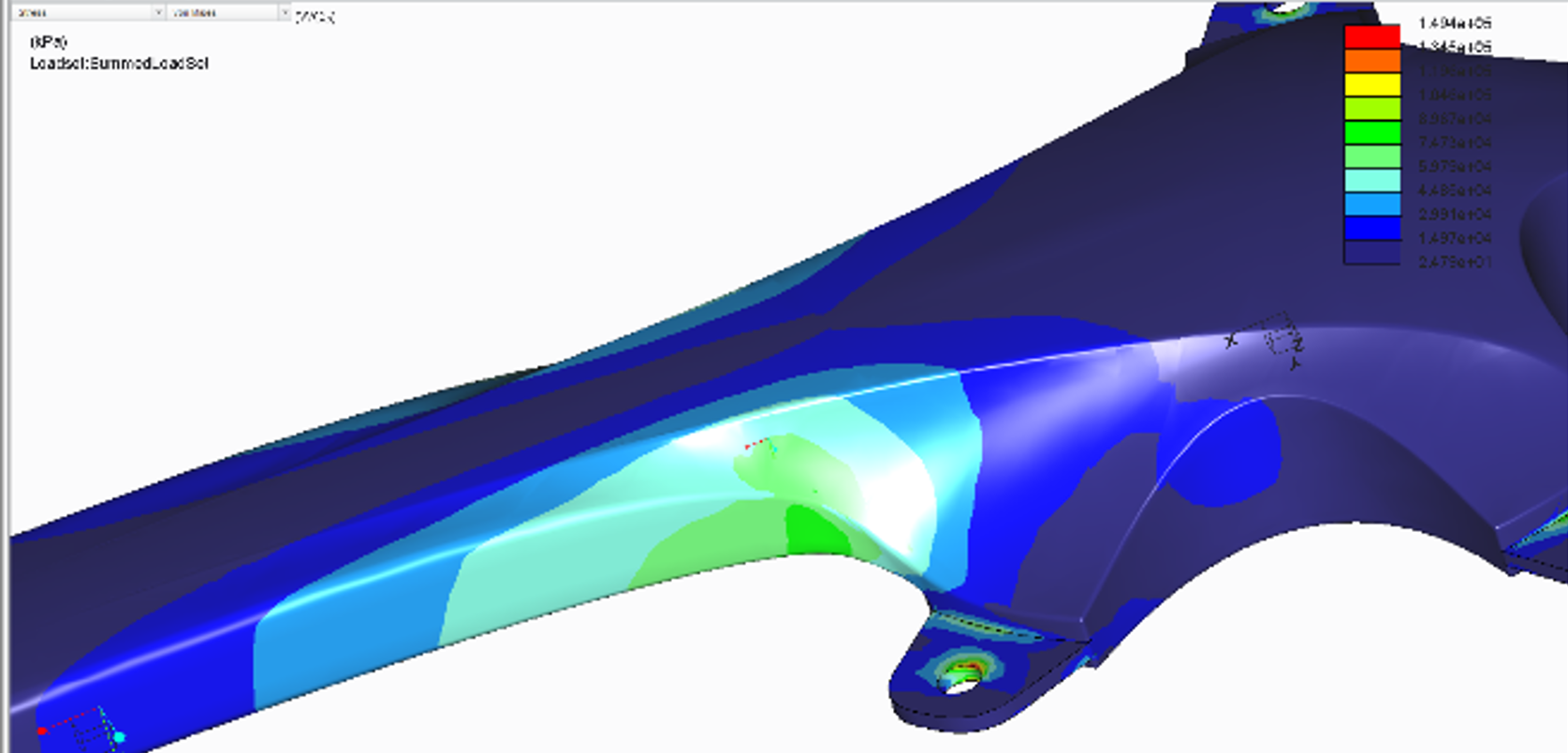
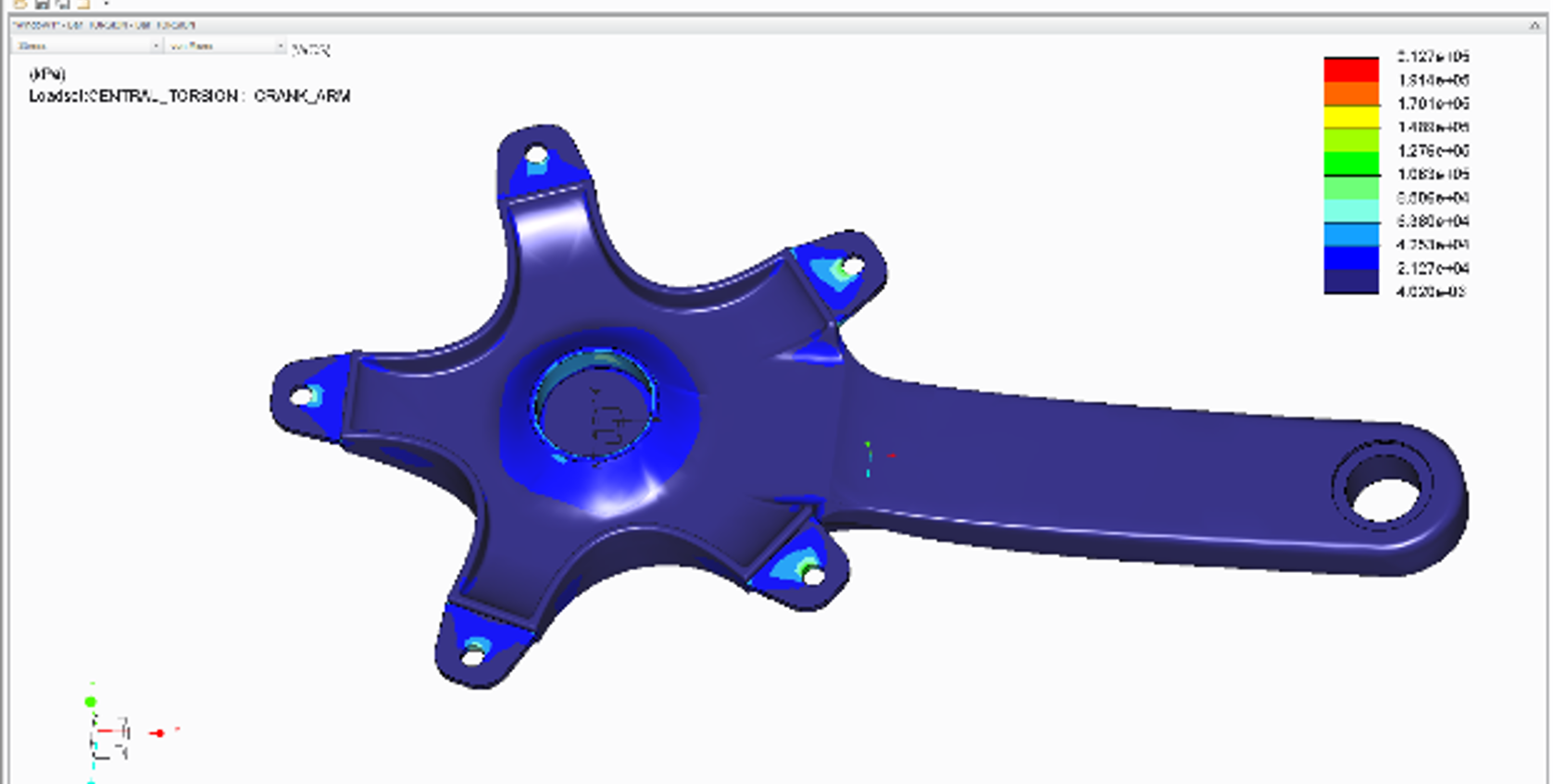
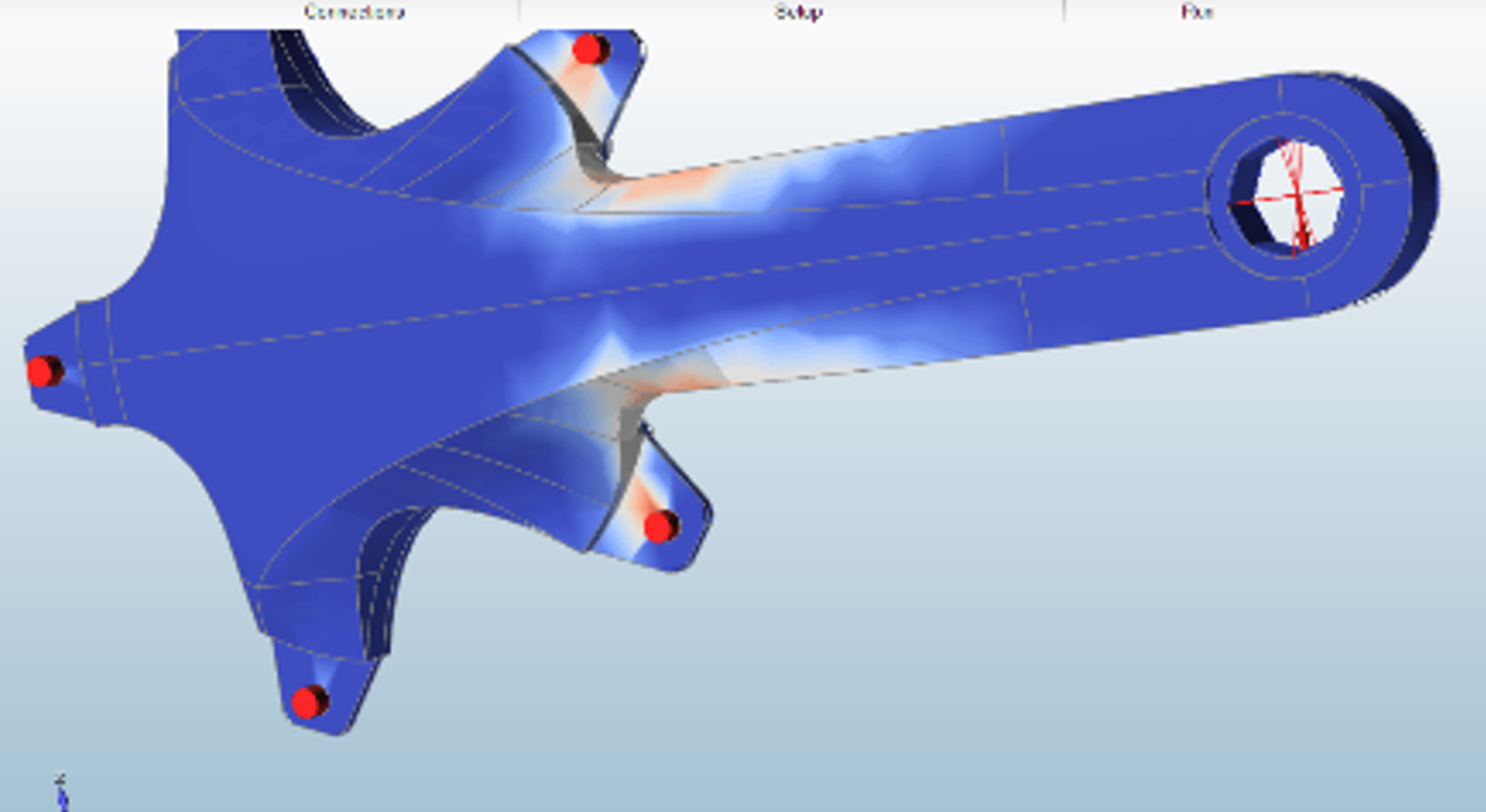
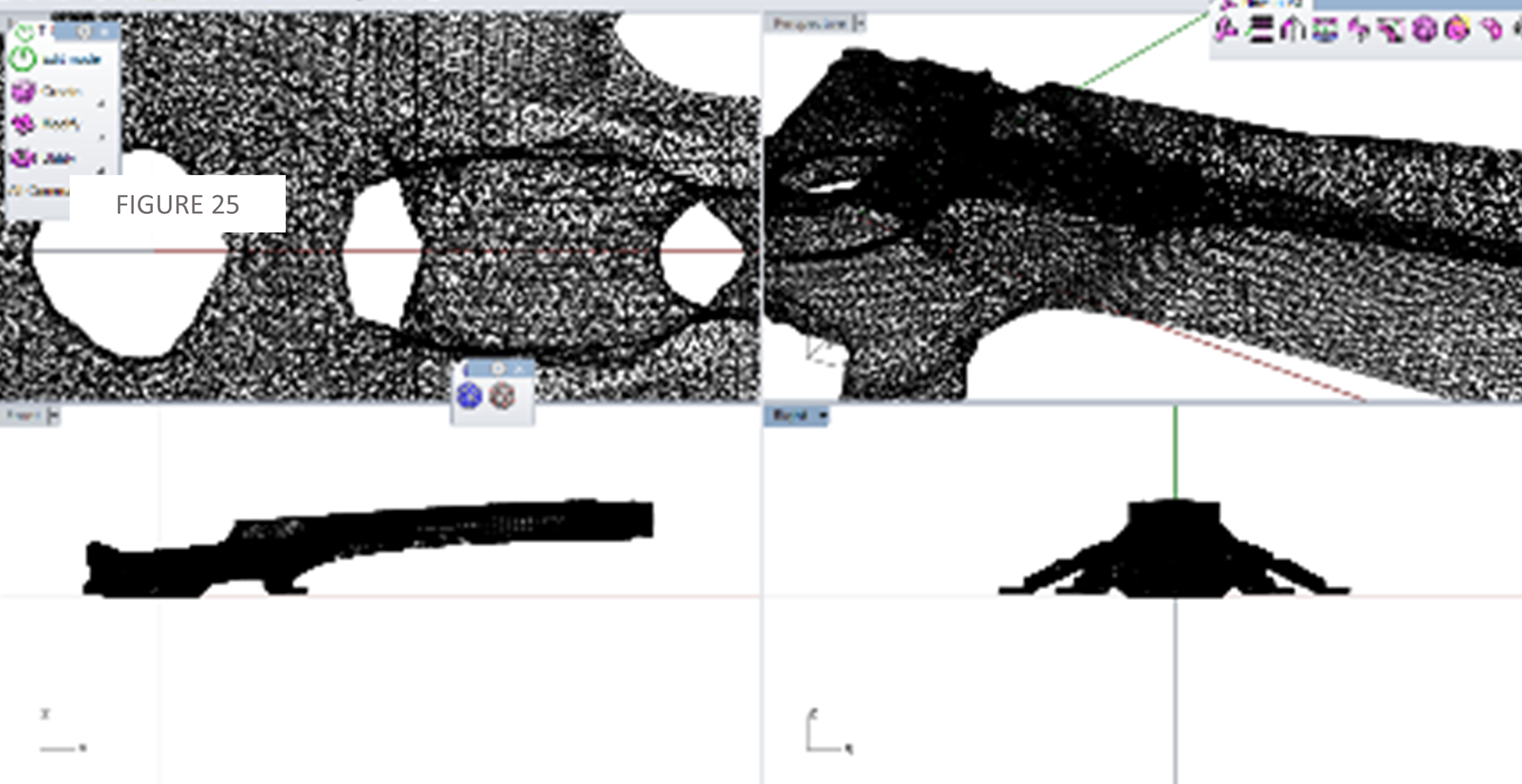
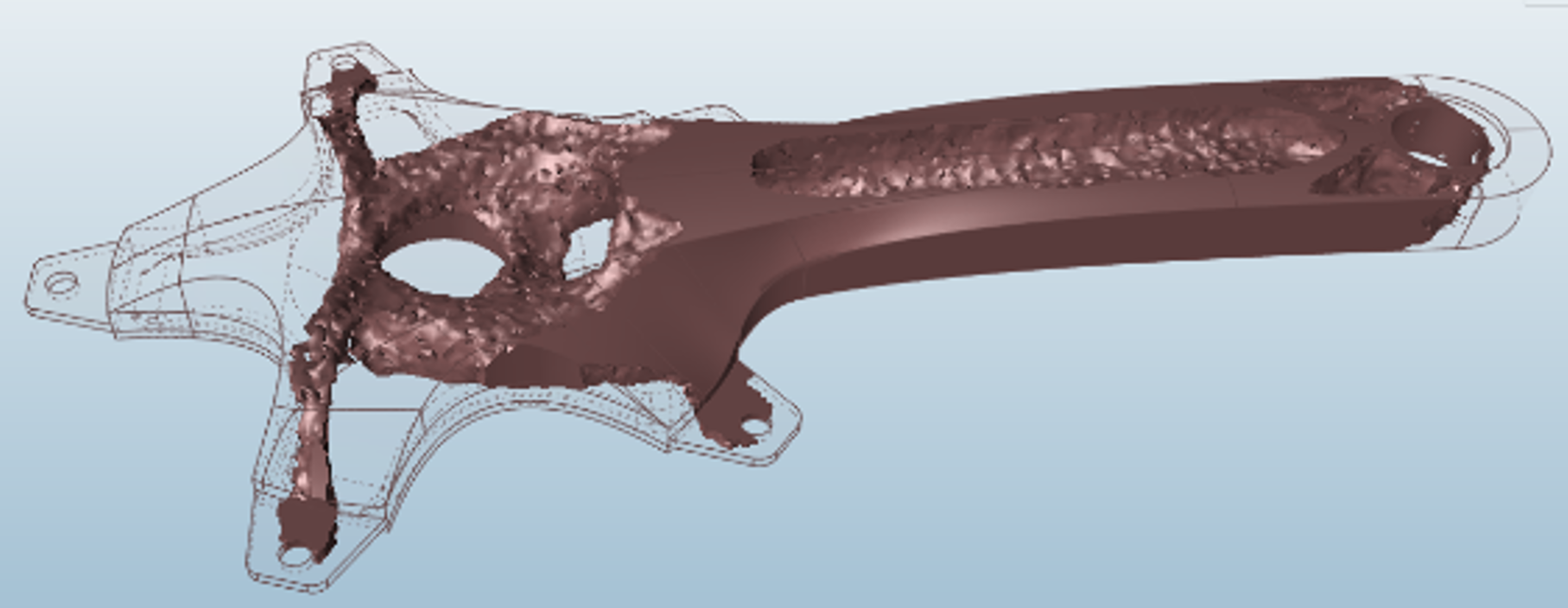
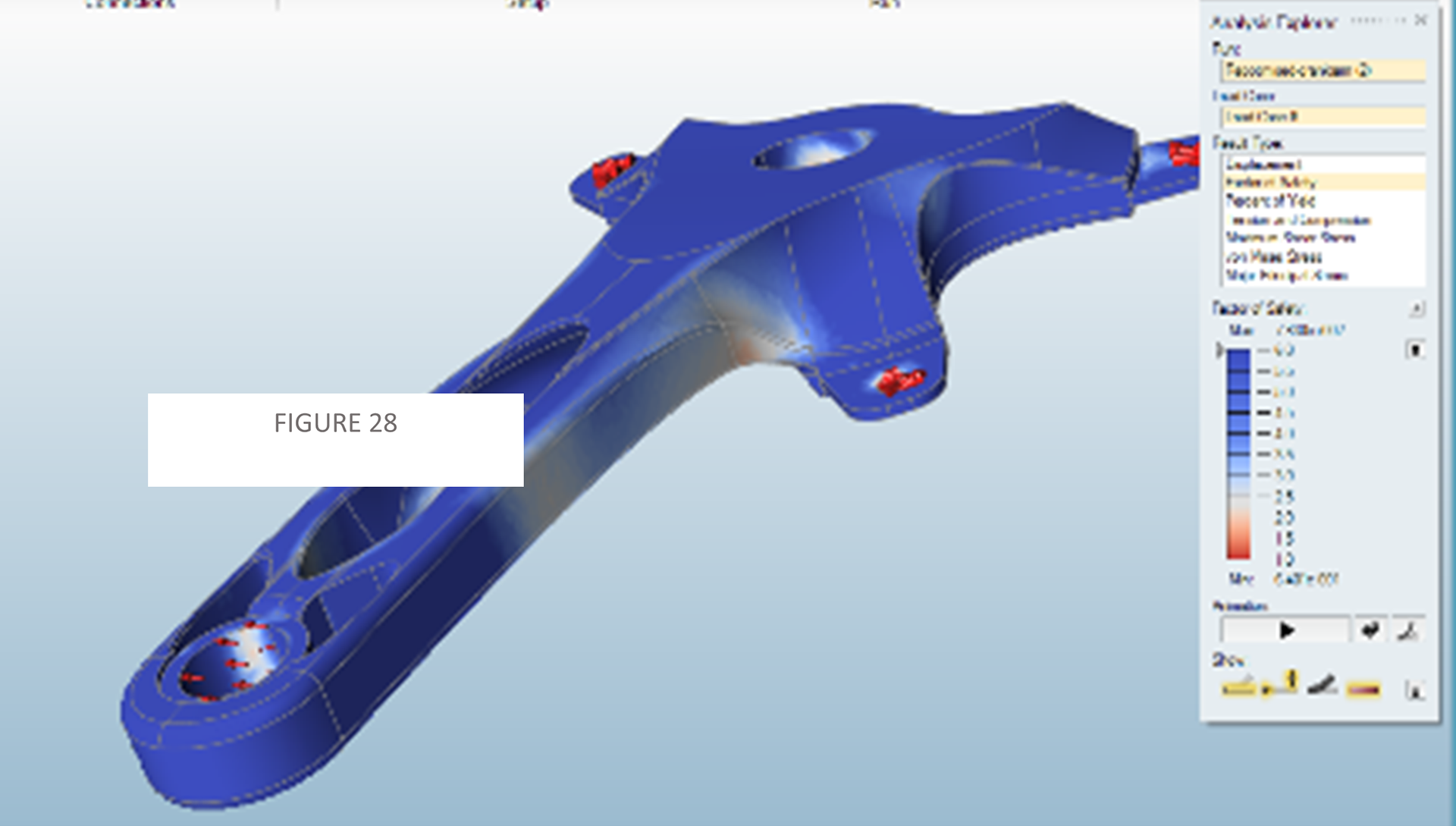
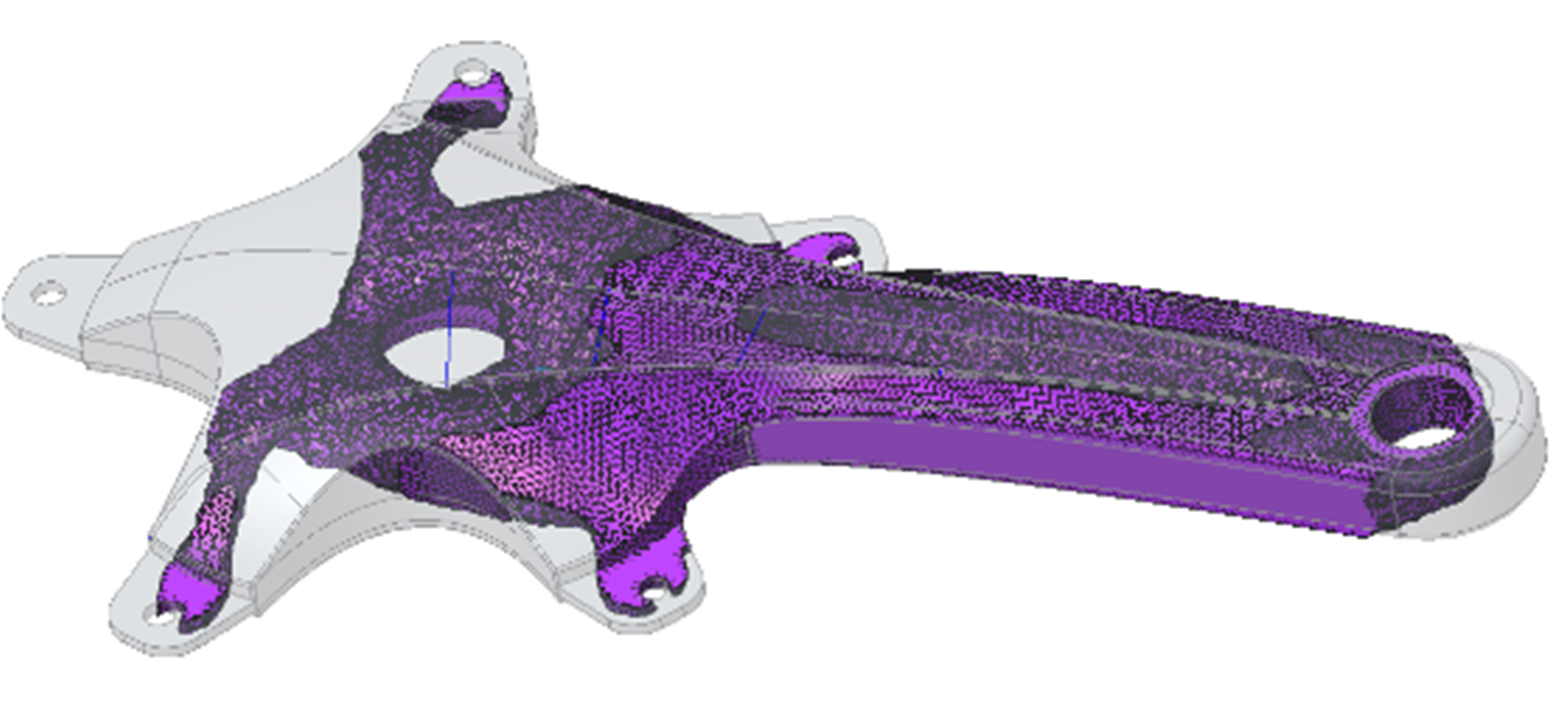
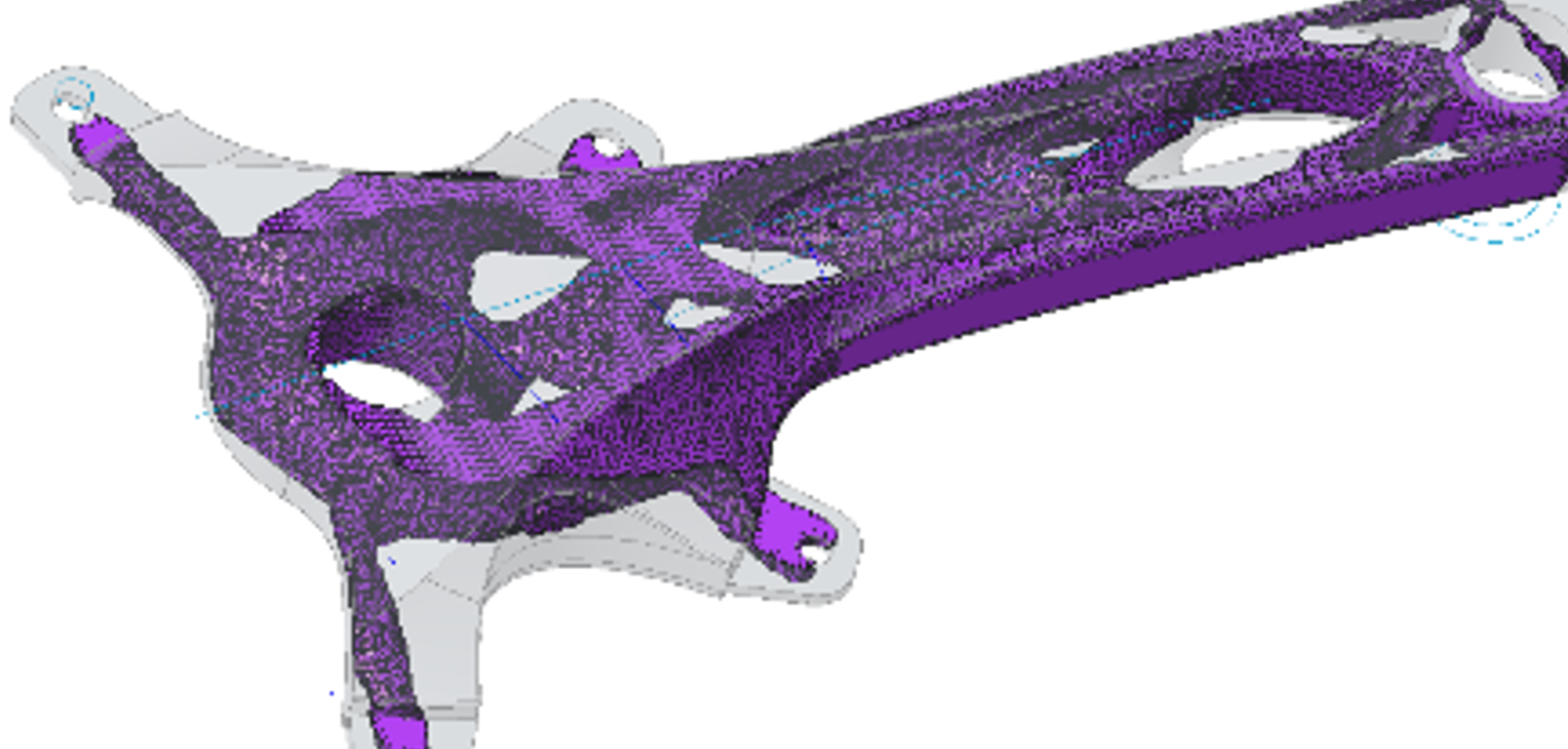
Rendering
Keyshot
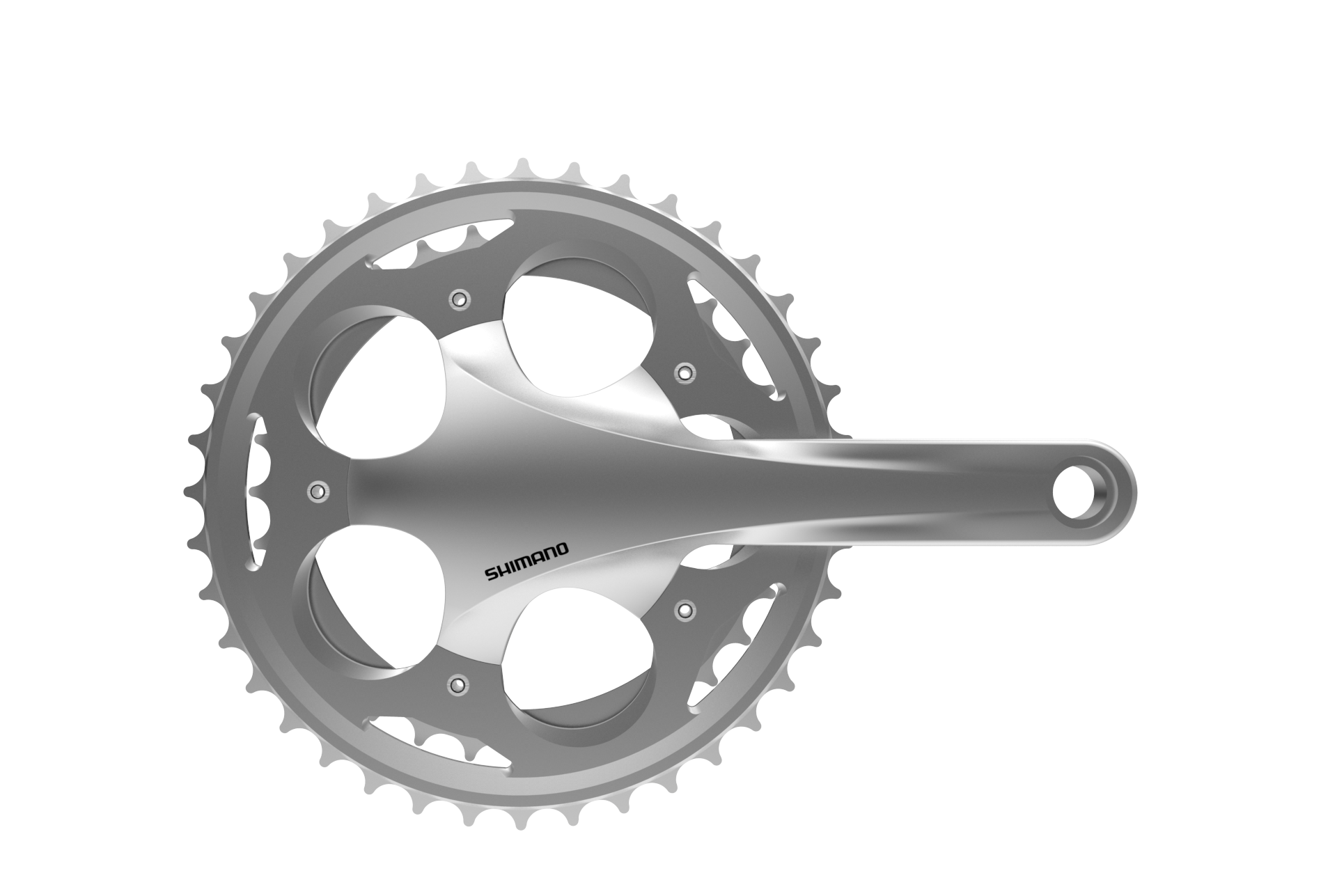
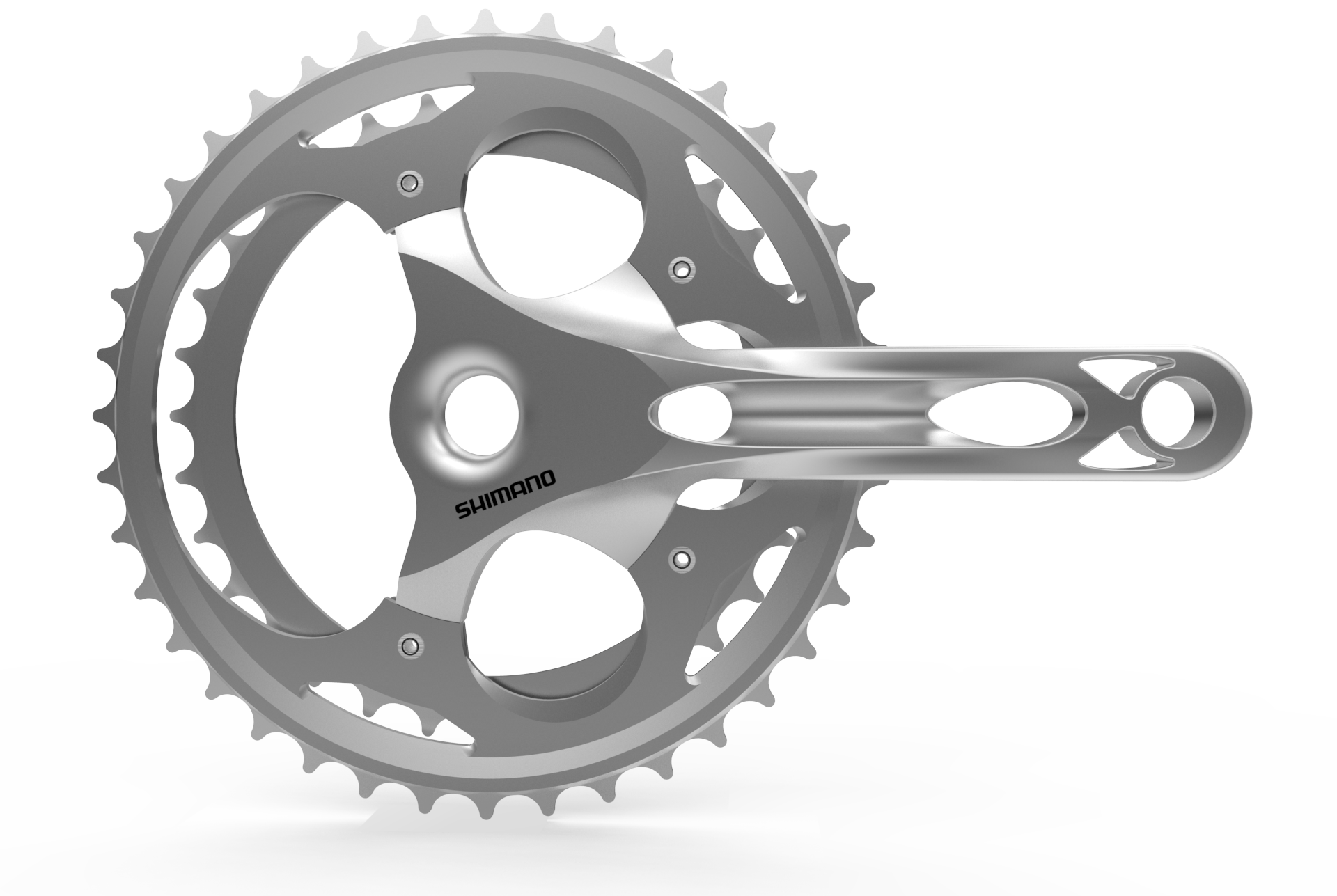
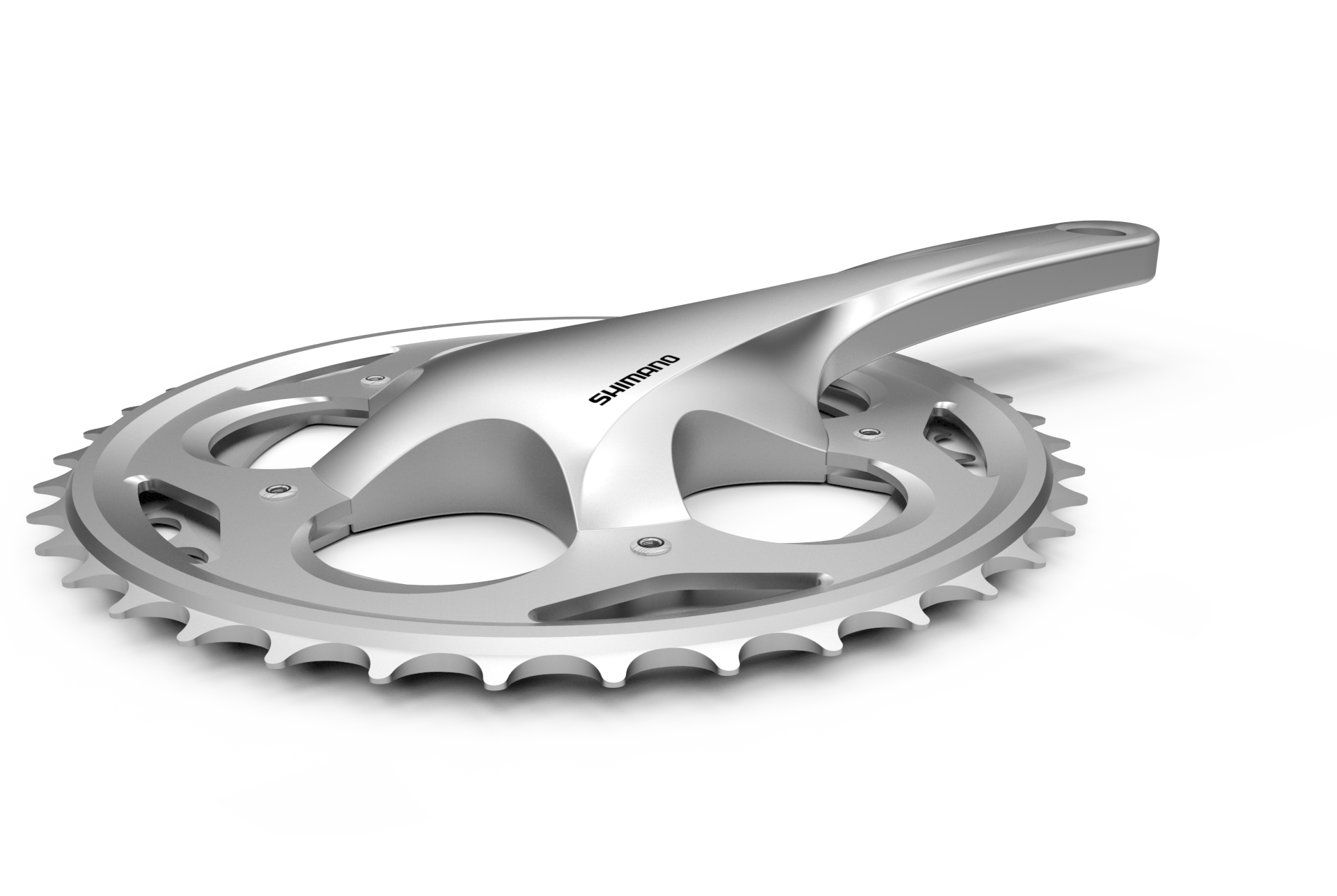
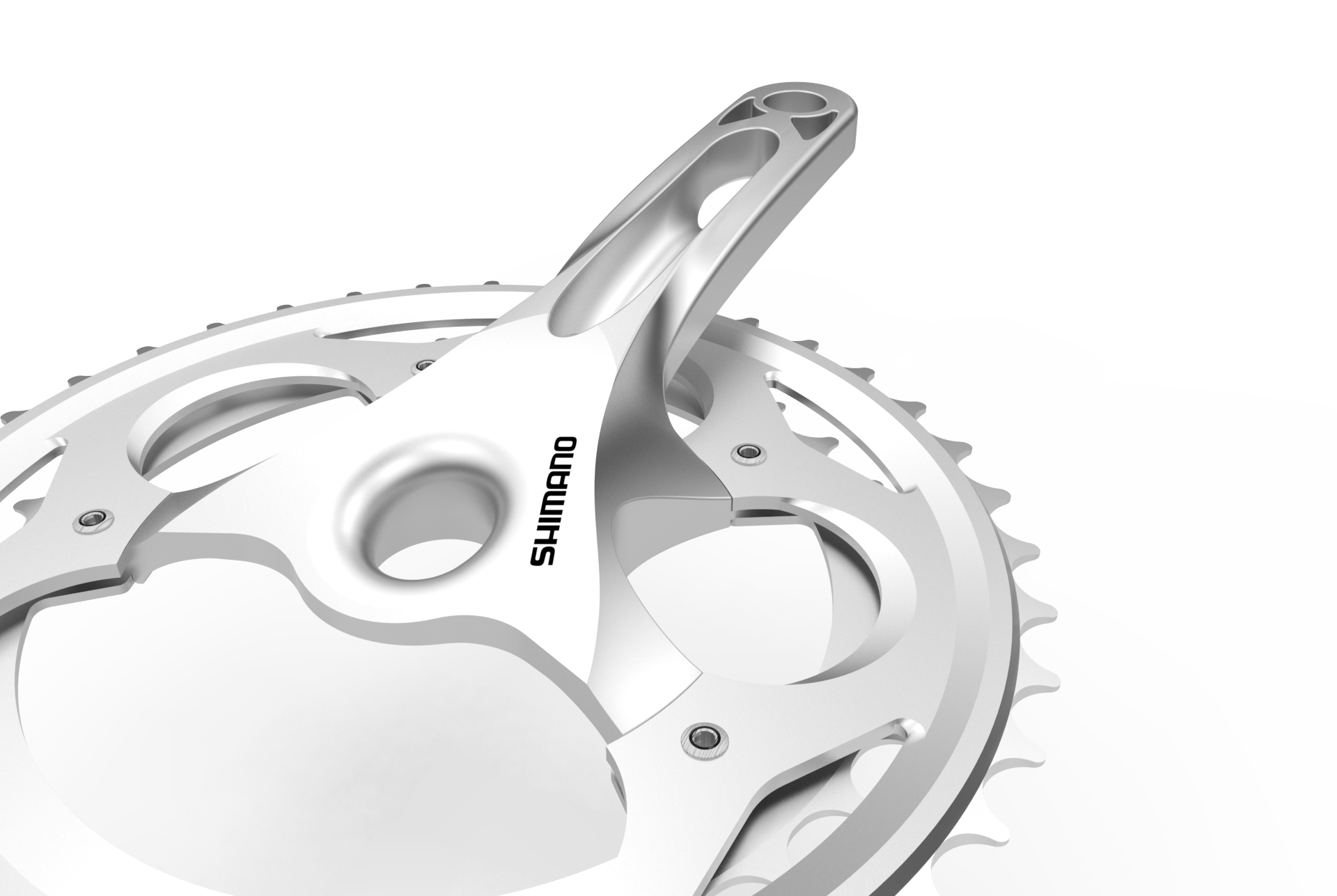
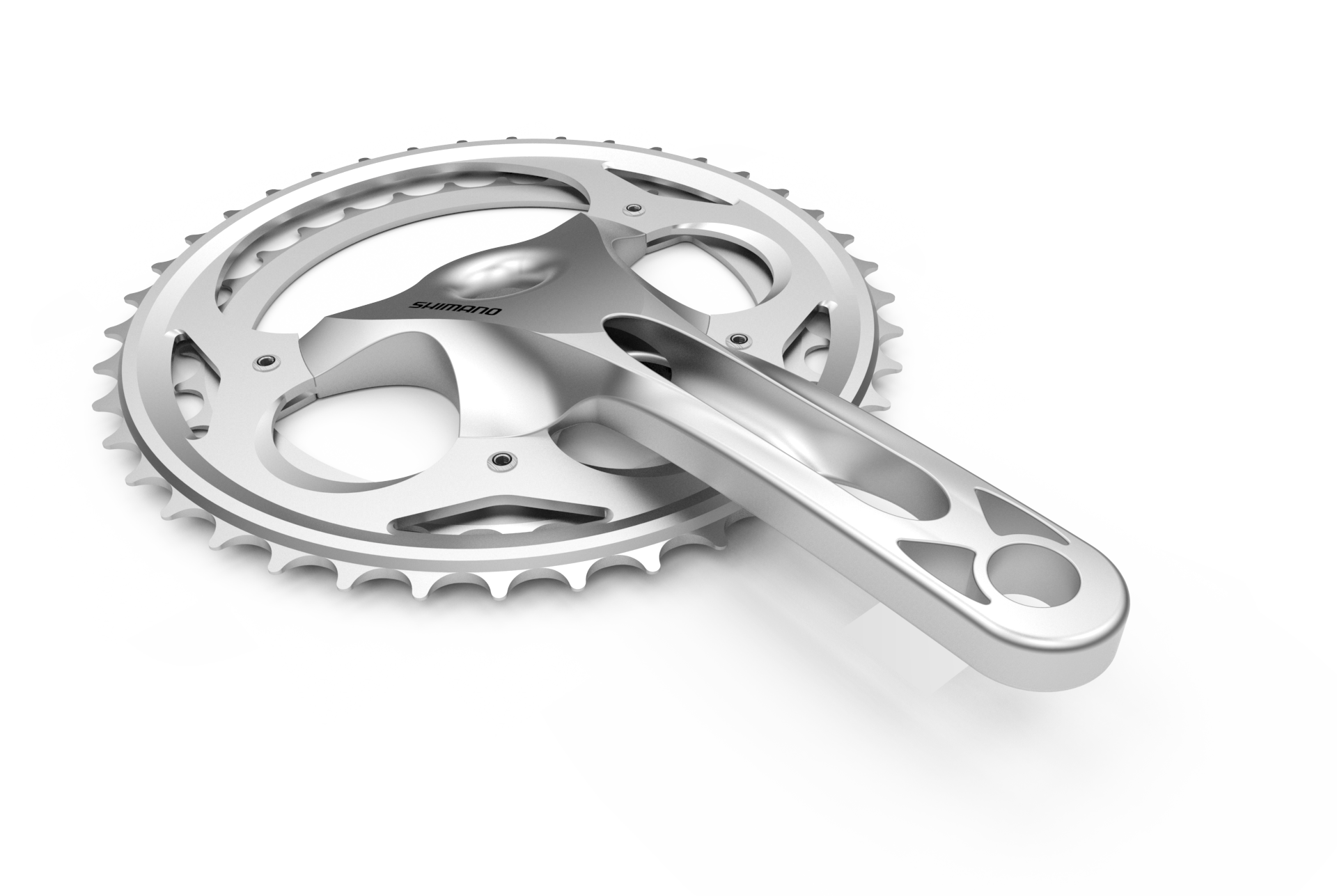
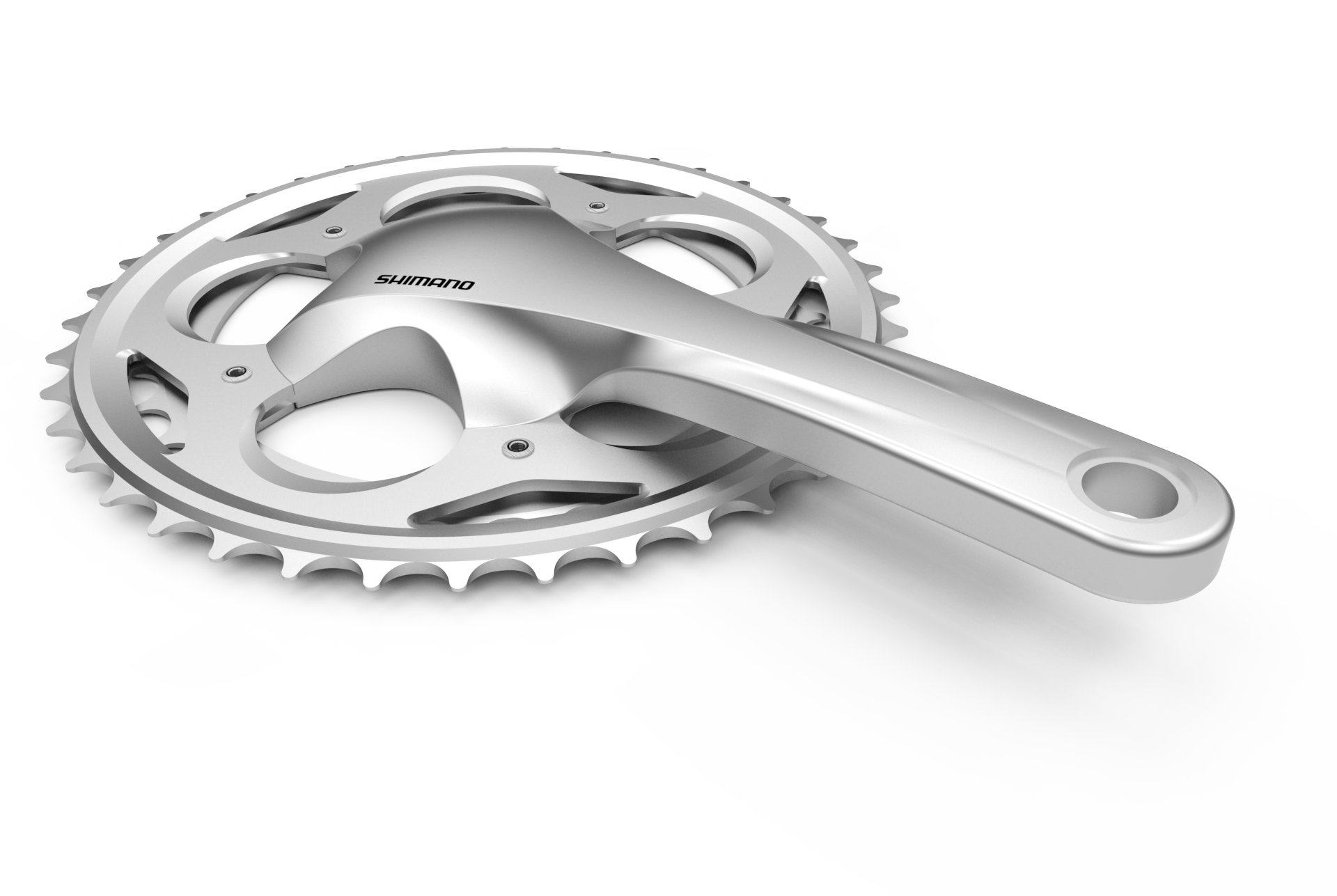
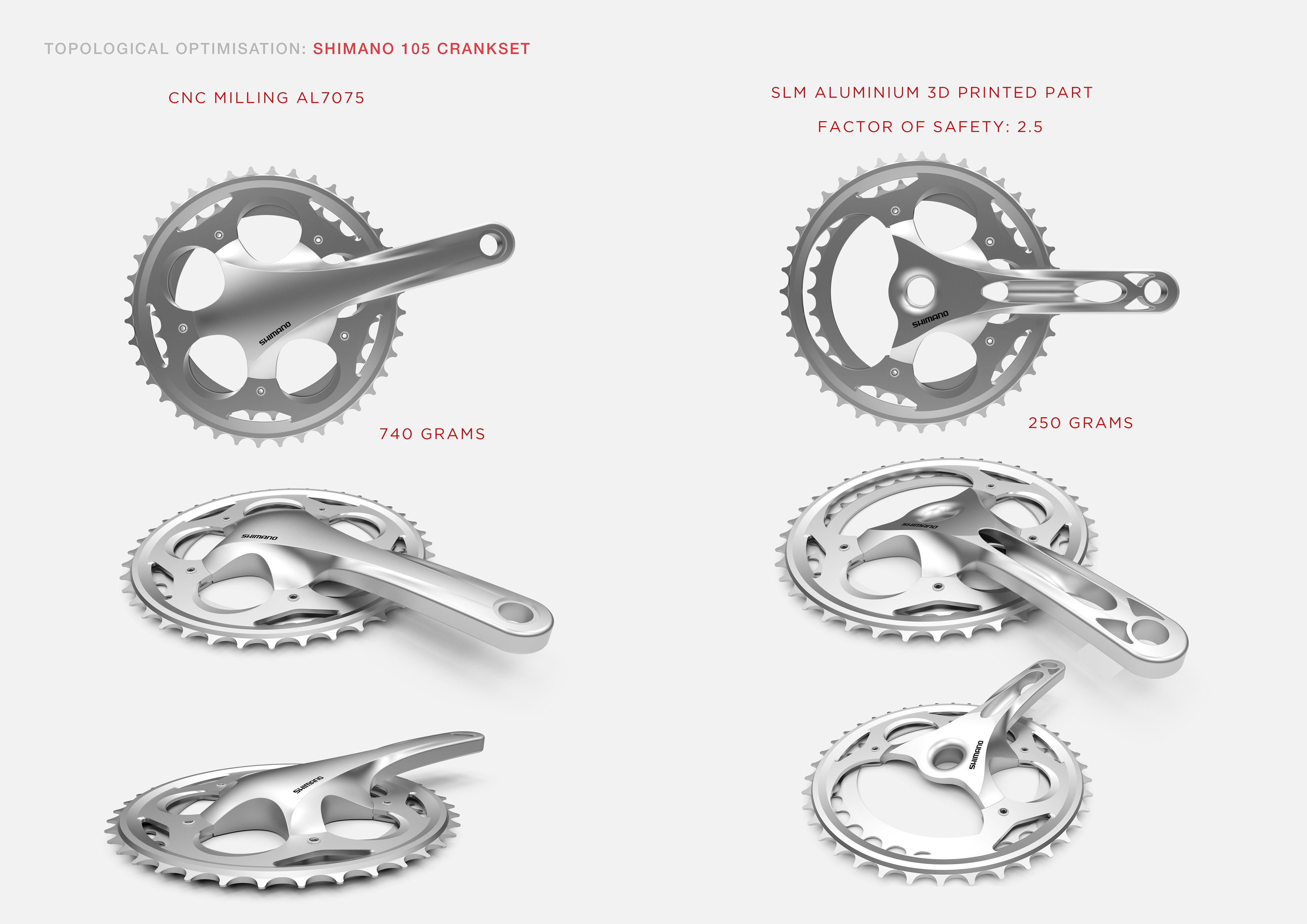
Final Result
A few months after completing the project, Shimano serendipitously came up with crankset with the same 4-spoke design that the topological optimization showed as the best design choice. I was really happy with the results of the project and learnt a huge amount surface modelling with mixed CAD in the process.
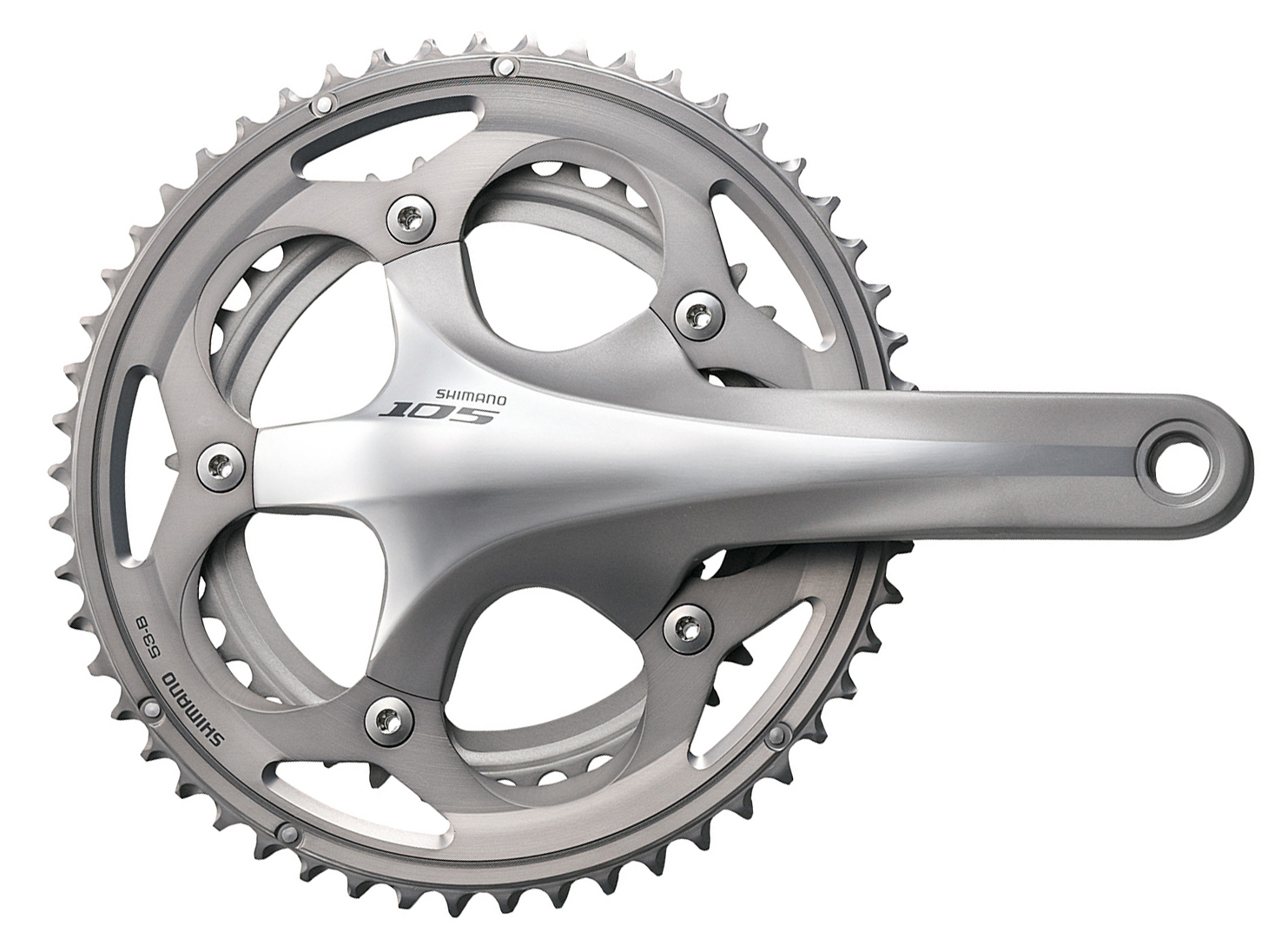
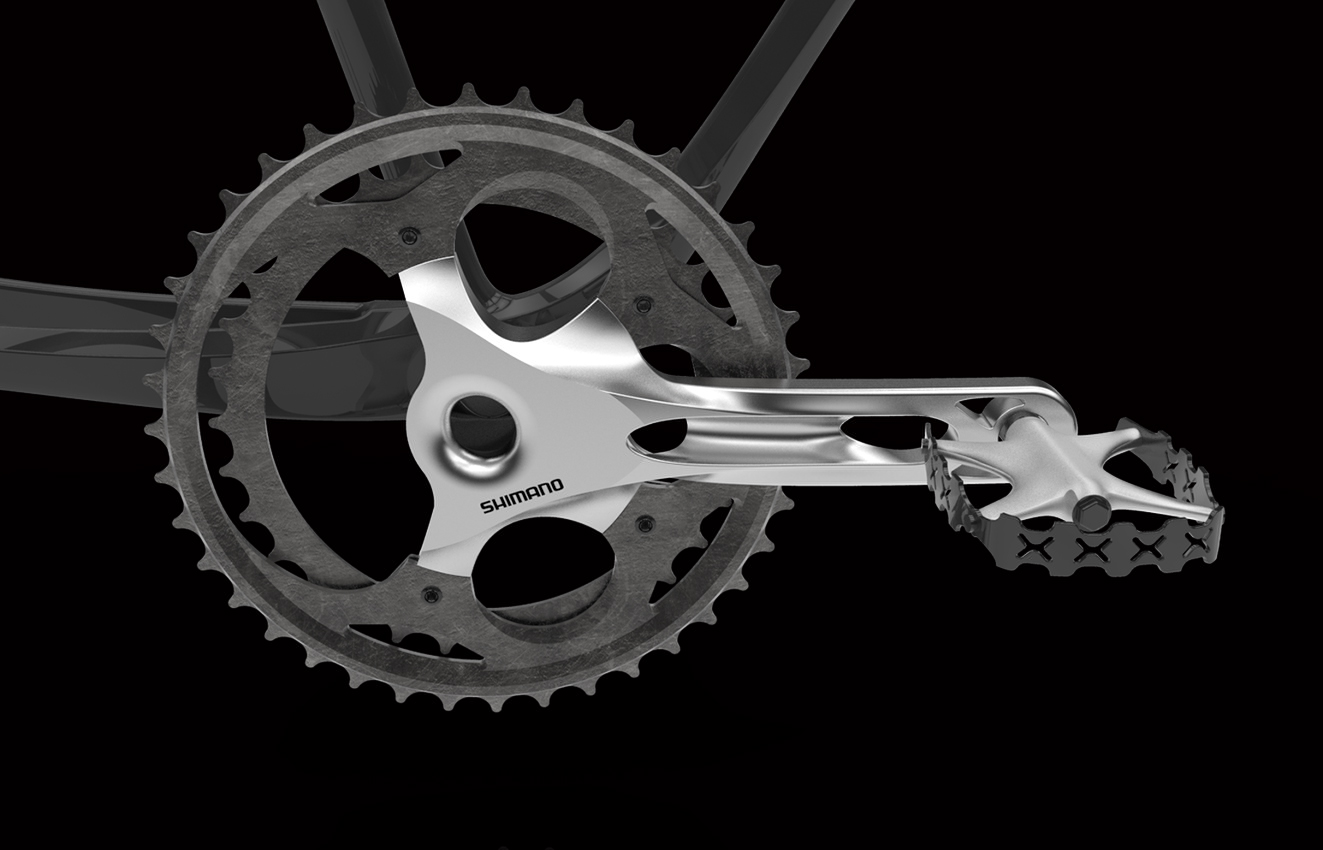
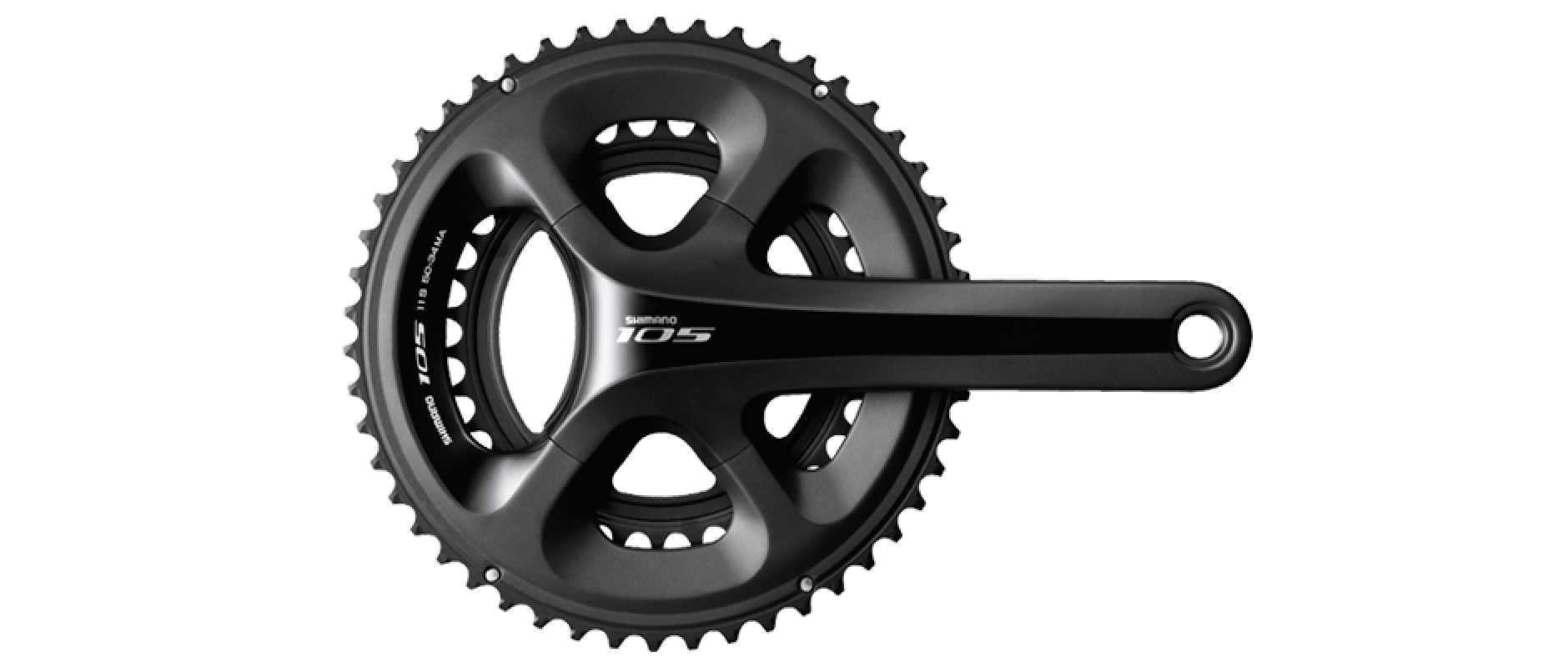