From one into three
From the 2015 bluefin drive, we built three entirely new drives packed with innovation. I led the MDGT and MD180 development programs.
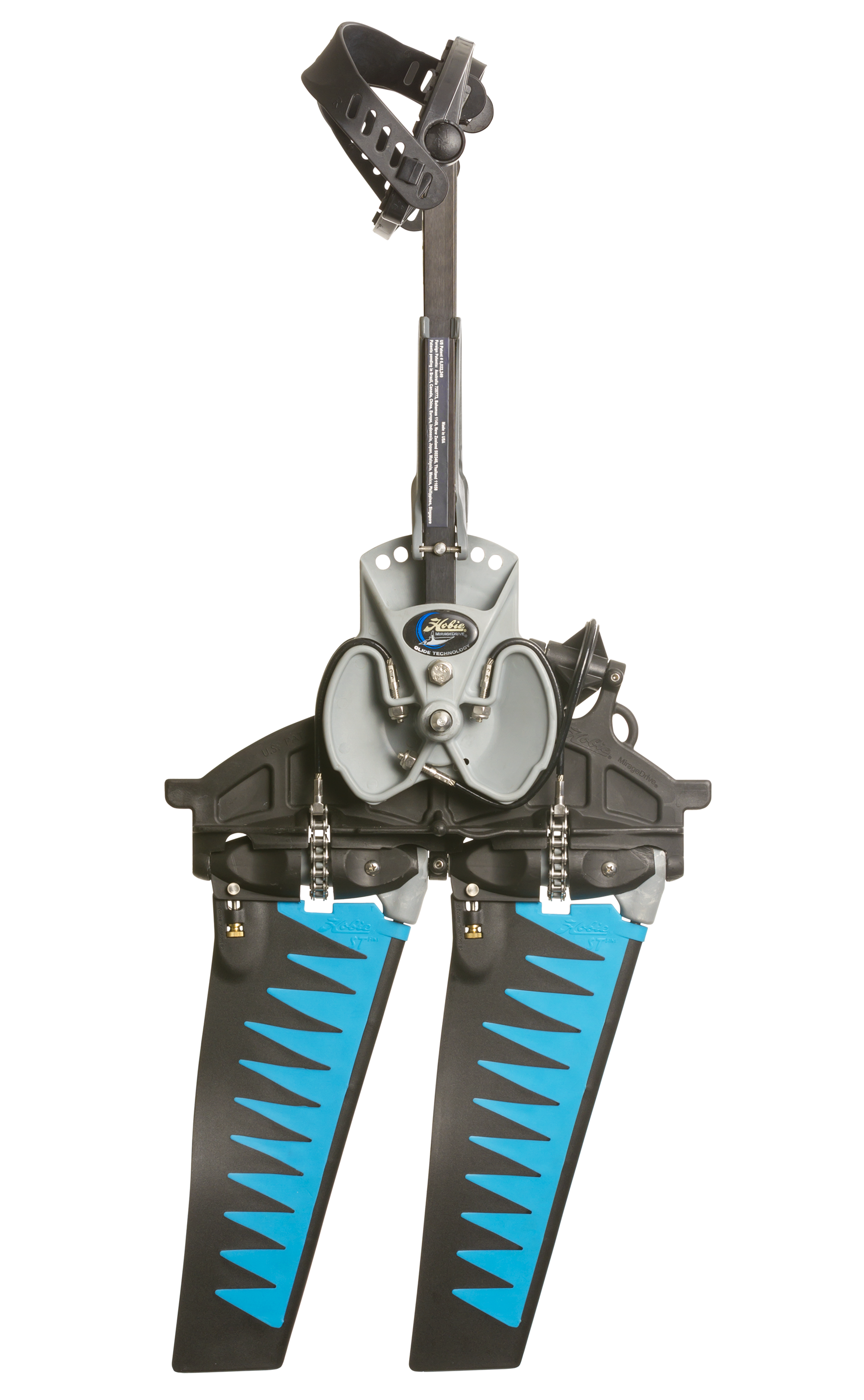
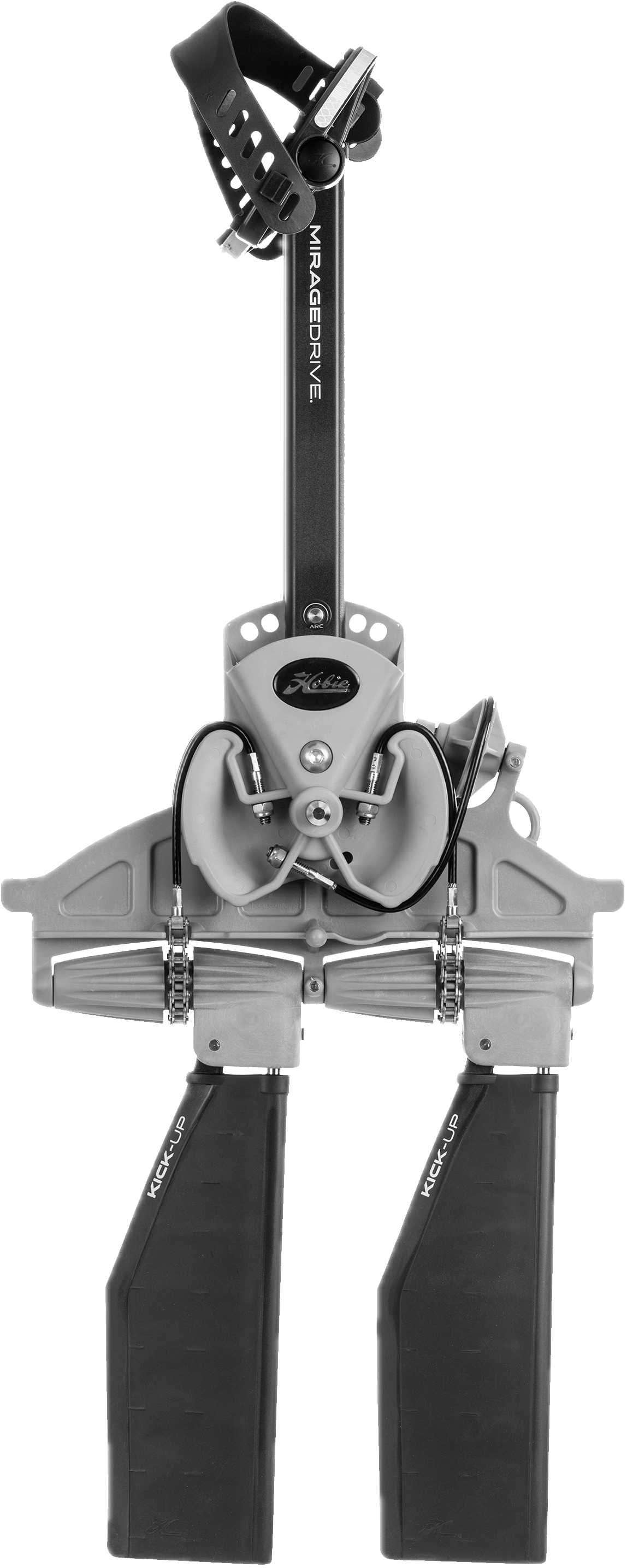

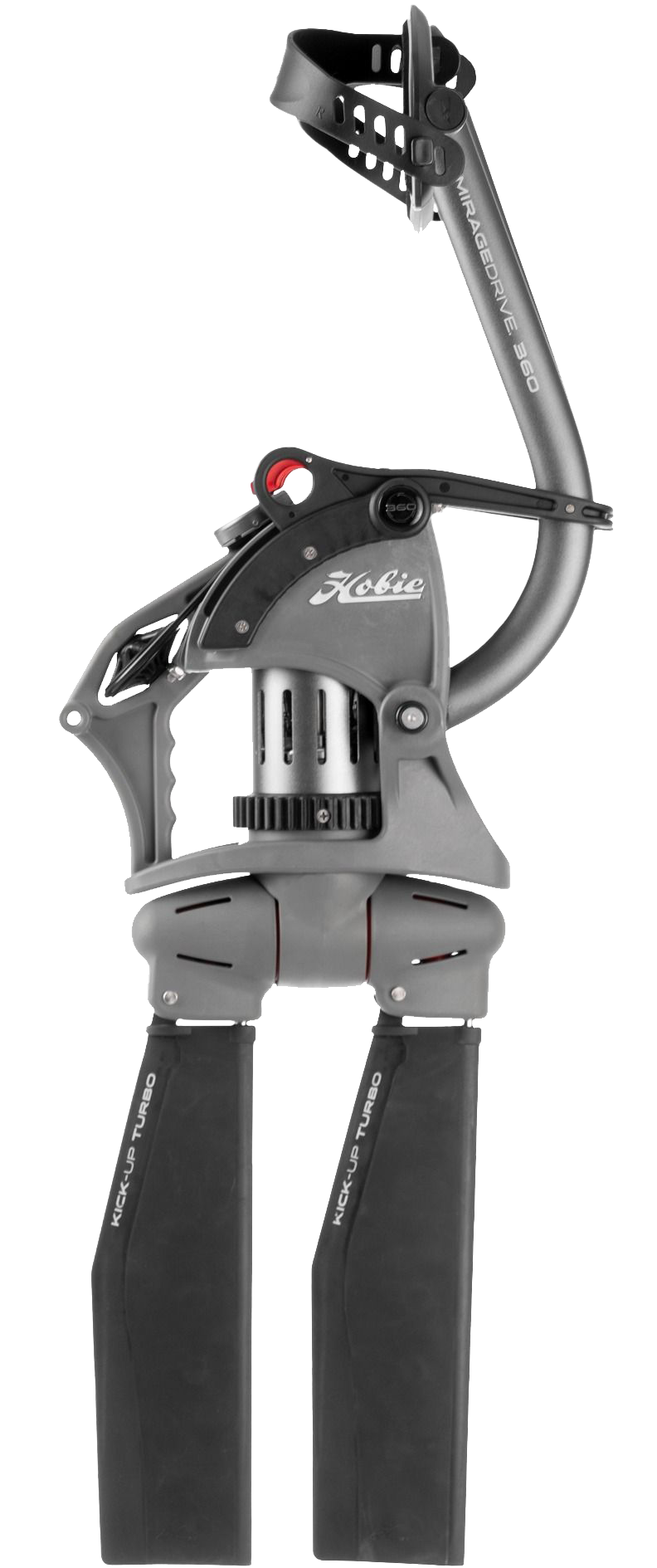
Reversing Kick-Up fins
The patented US9359052 design enables all three drives to hit underwater objects without breaking the drive. Kick-Up fins reduced warranty failures by 95%. The shape of the new fin design increased thrust and reduced strain on the overall drive system, doubling the miles pedaled before fatigue failure.
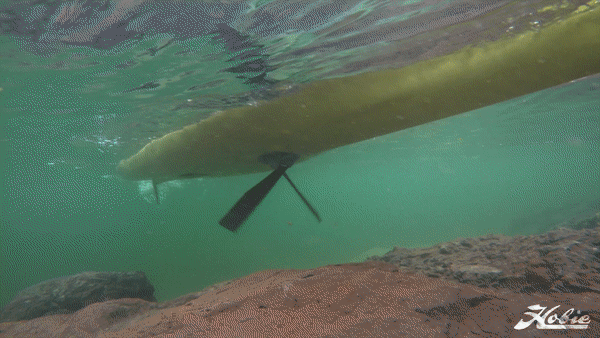
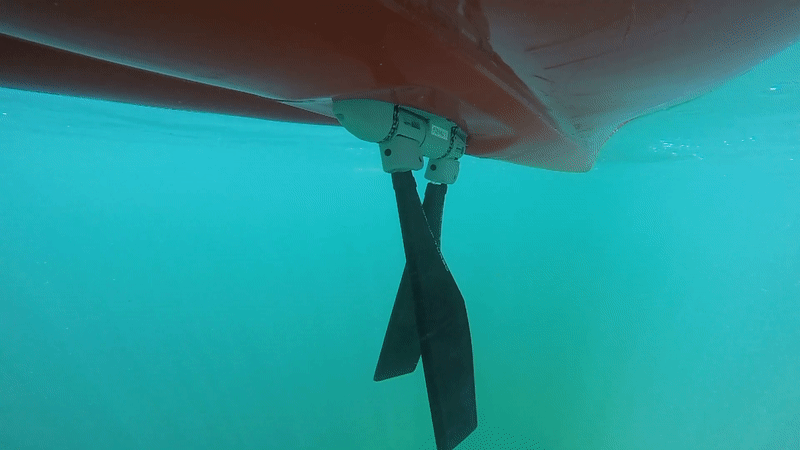
User-focused invention
MirageDrive pedals are adjustable to fit different leg lengths. I patented a new mechanism US10005531 inside the hollow crank that allows a push button to adjust the position of the crank. This design made adjusting the crank immediately obvious to new users.
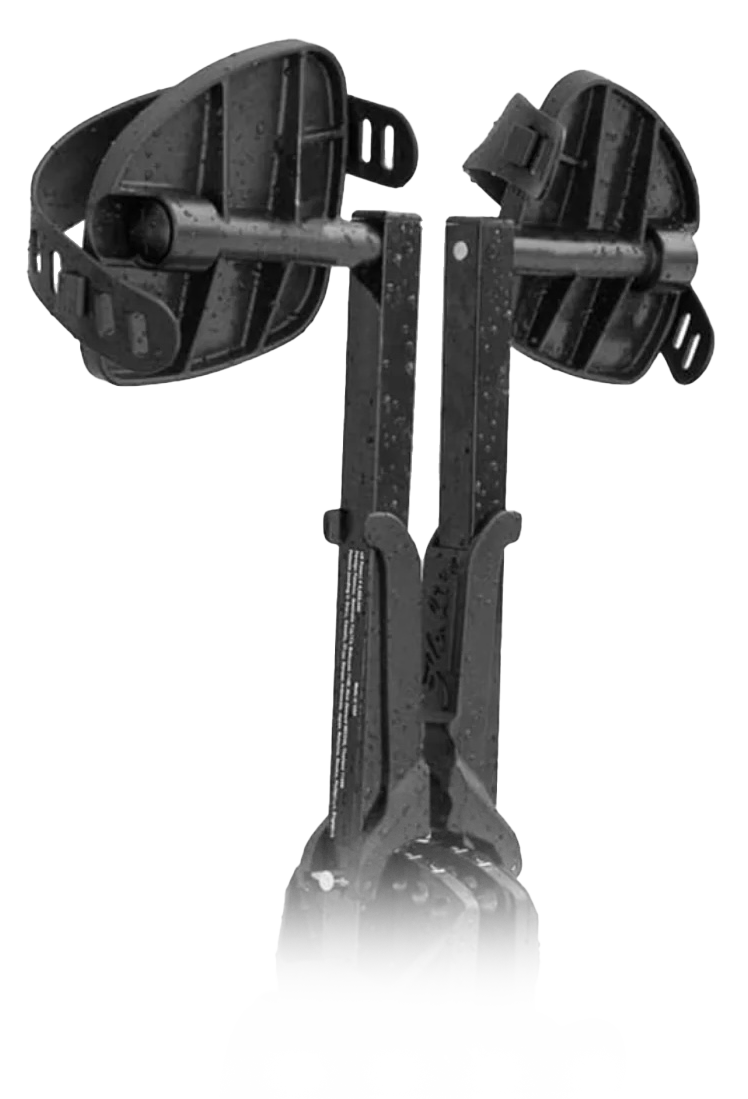
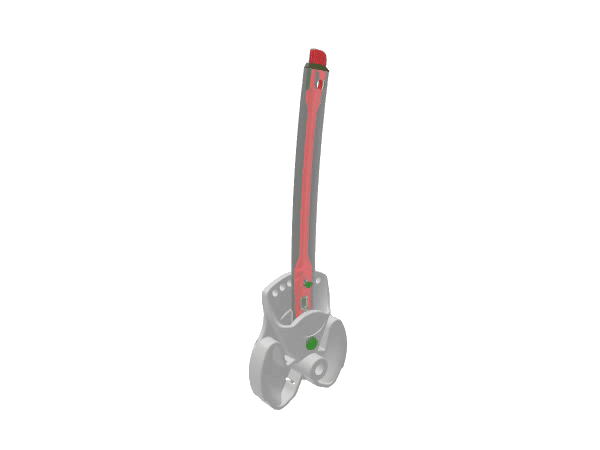
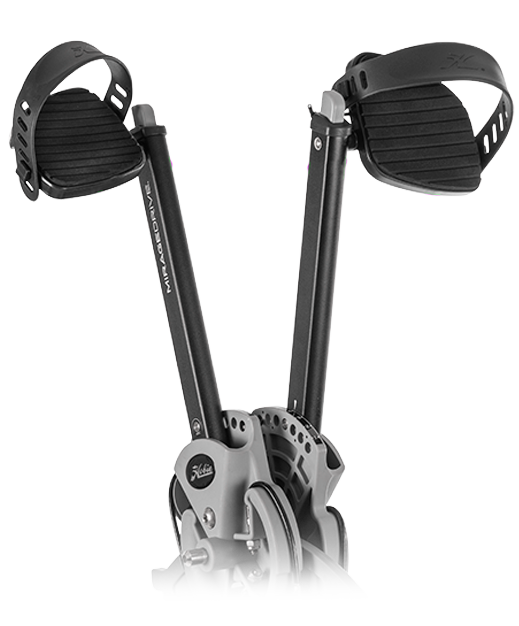
Sharing components
Using a top-down modeling strategy in SolidWorks allowed parts to be shared cross-platform decreasing cost and manufacturing risk. It was a huge challenge to integrate legacy components with new designs built in different factories.
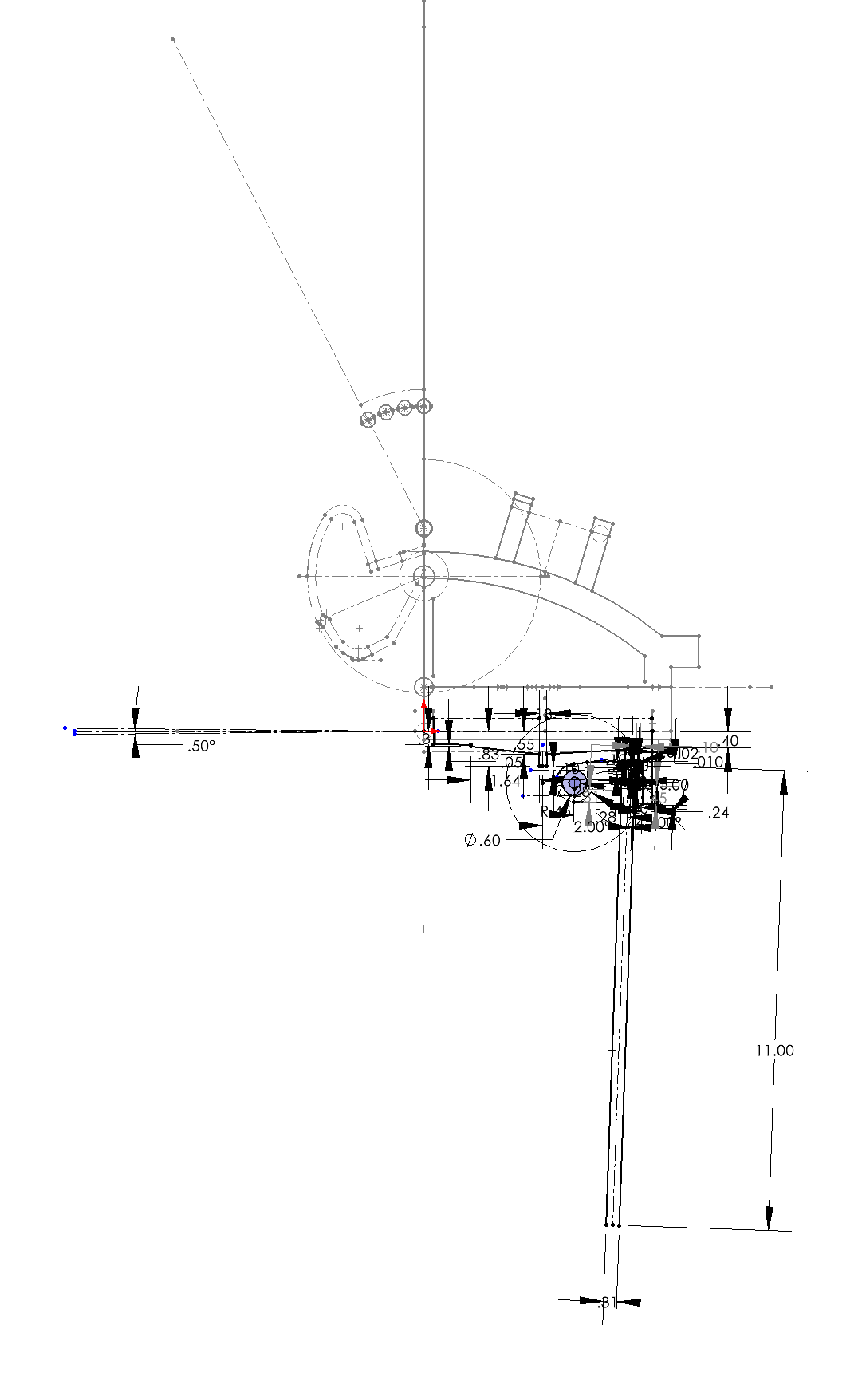
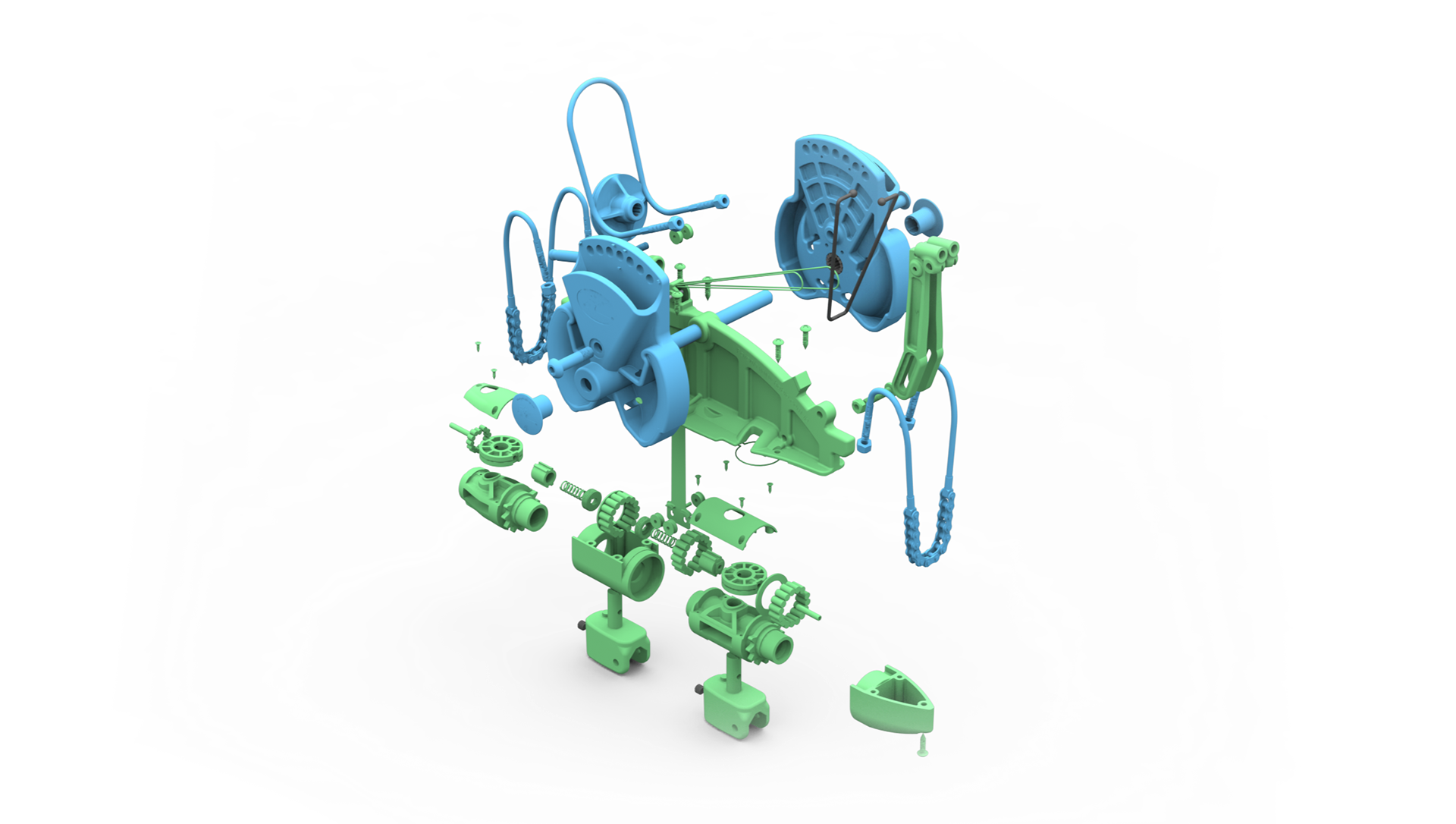
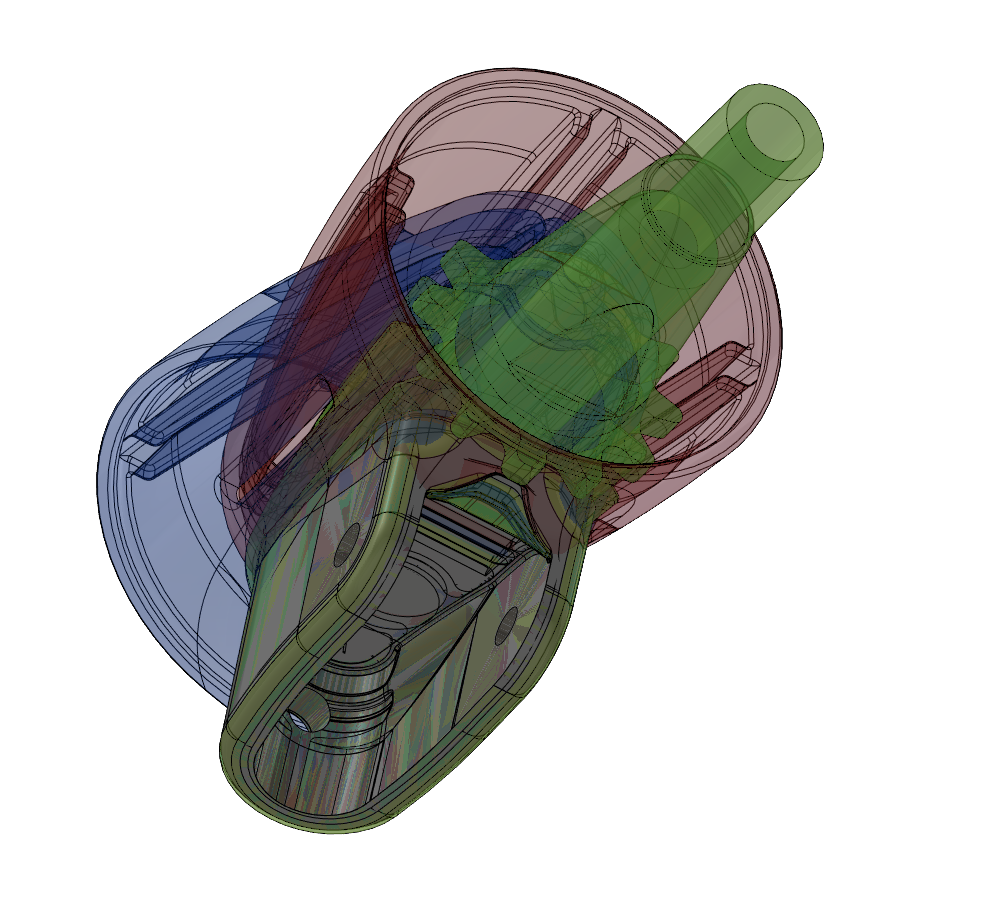
Good in theory
3D CAD, FEA, and rendering are useful, but they often don’t translate well from screen to reality. These initial engineering models provided the basic framework for building functional real-world prototypes.
I learned the hard way that going from a square crank to a round crank negatively affected the torsional stiffness of the crank. I had chosen user carrying comfort over a better engineering structure for pedaling. I had to quickly come up with a new solution to meet our deadlines for release. We had already made initial tools, and extrusion dies.
I redesigned the crank to have greater stiffness that any other design by going with a rectangular shaped extrusion. It was a huge success. It improved ergonomics, stiffness and even the stamping process for forming the holes exactly.
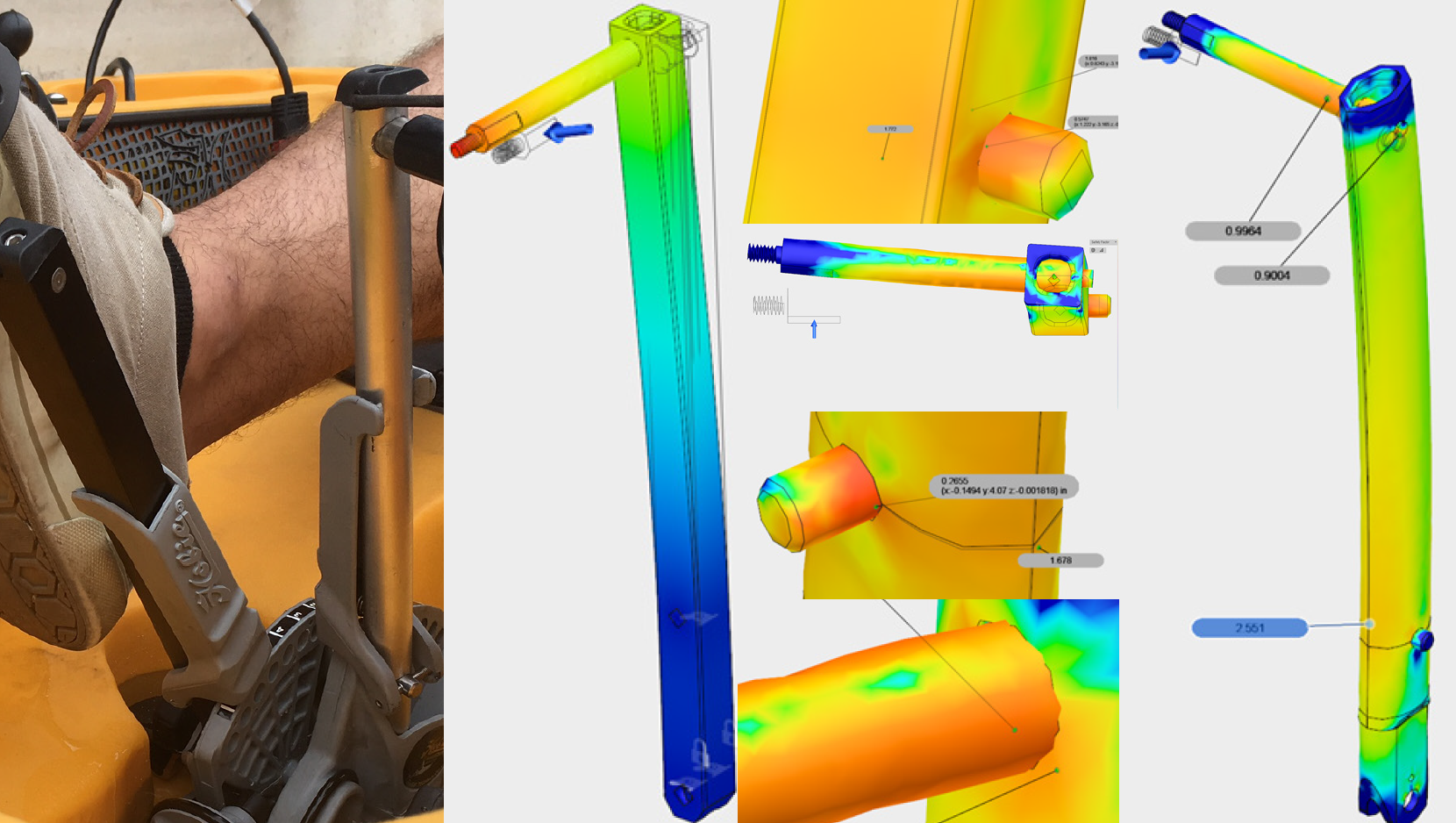
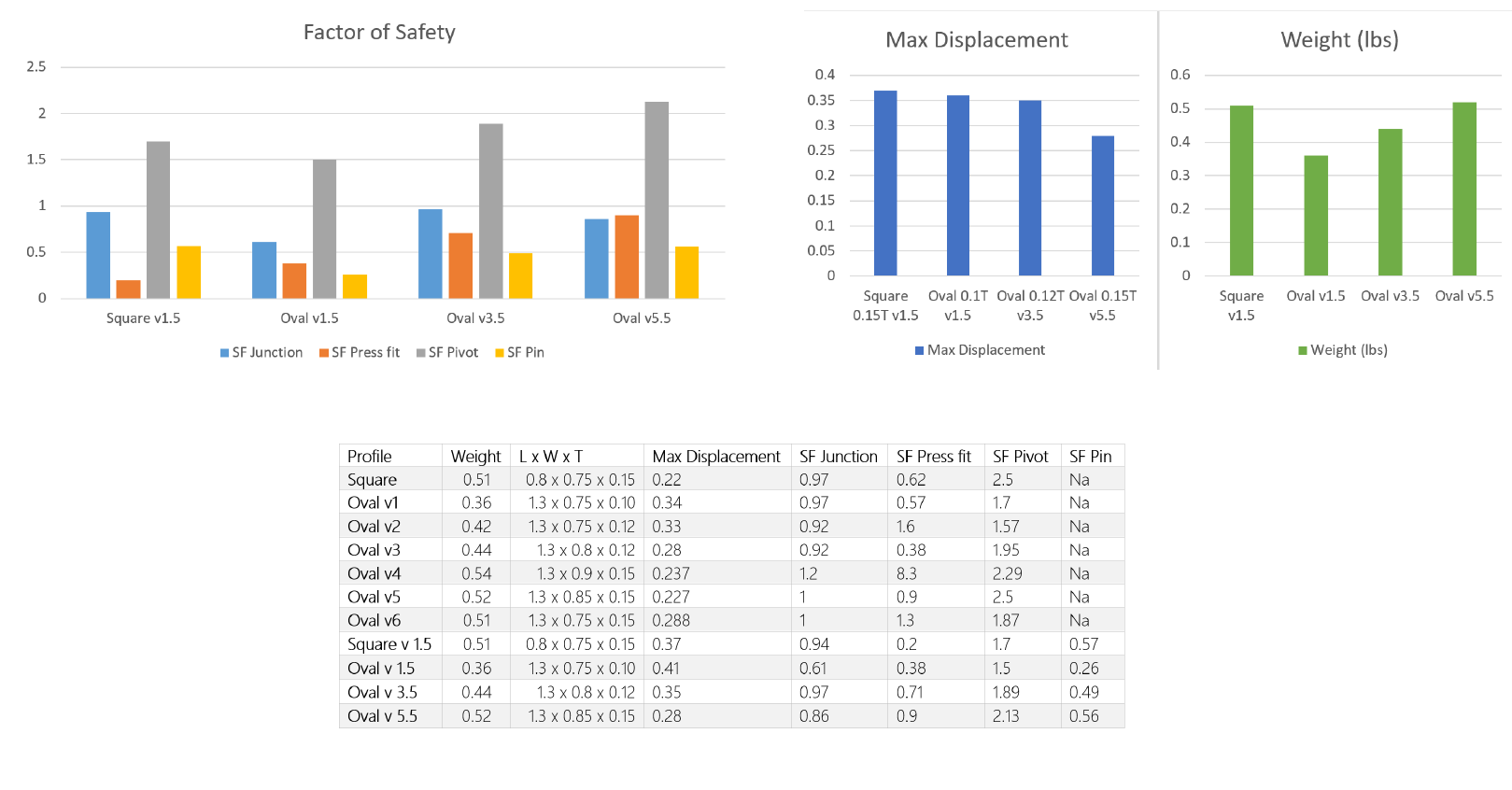
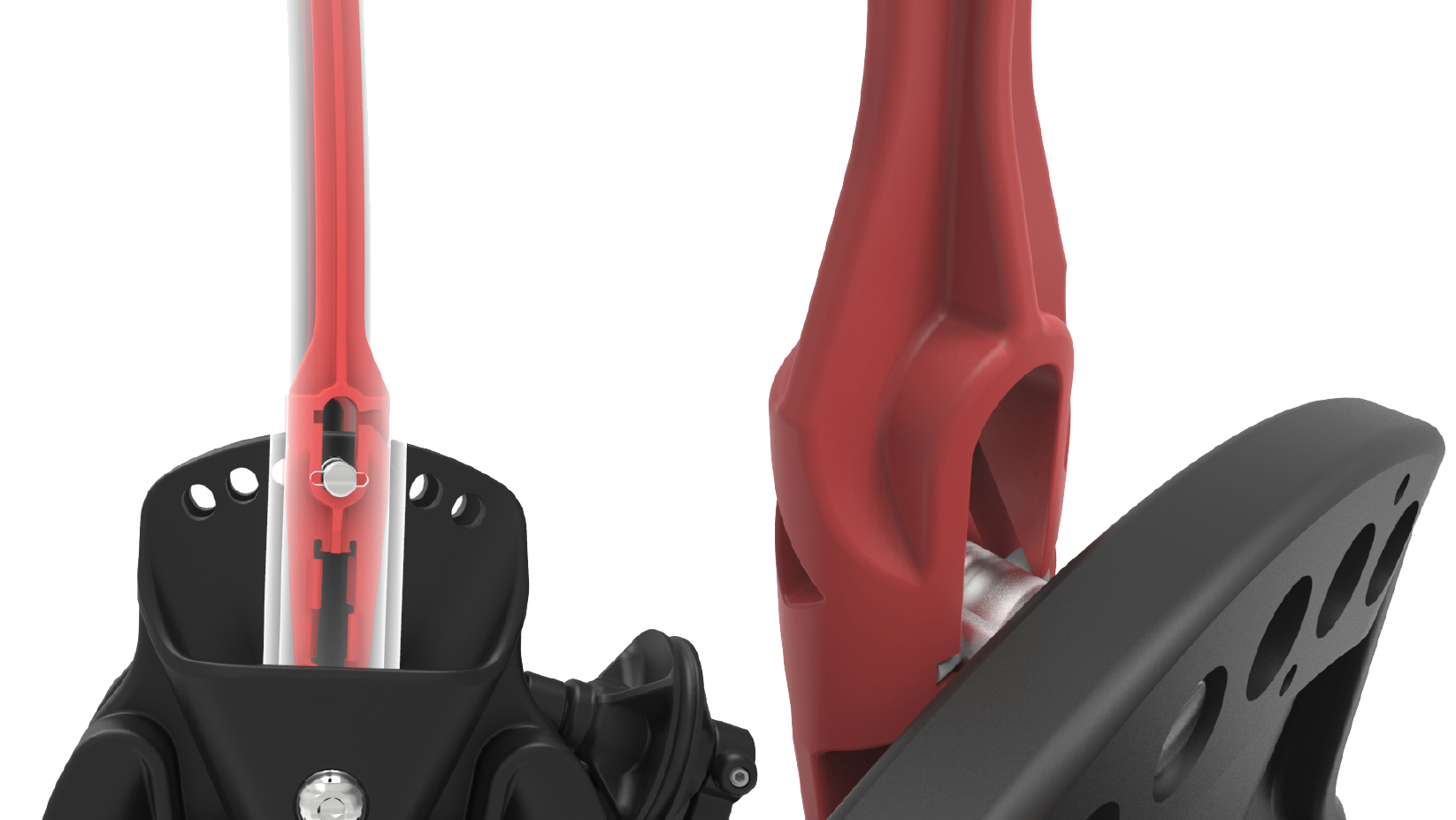
SolidWorks FEA • Keyshot
Test to failure
A thorough testing phase exposed design issues in real-world scenarios. I recruited professional testers and put thousands of miles on drives in different locations around the world. We also created cycle testers for drives to simulate millions of miles in a few weeks.
Sand test chains
Cycle testing
Fin warp
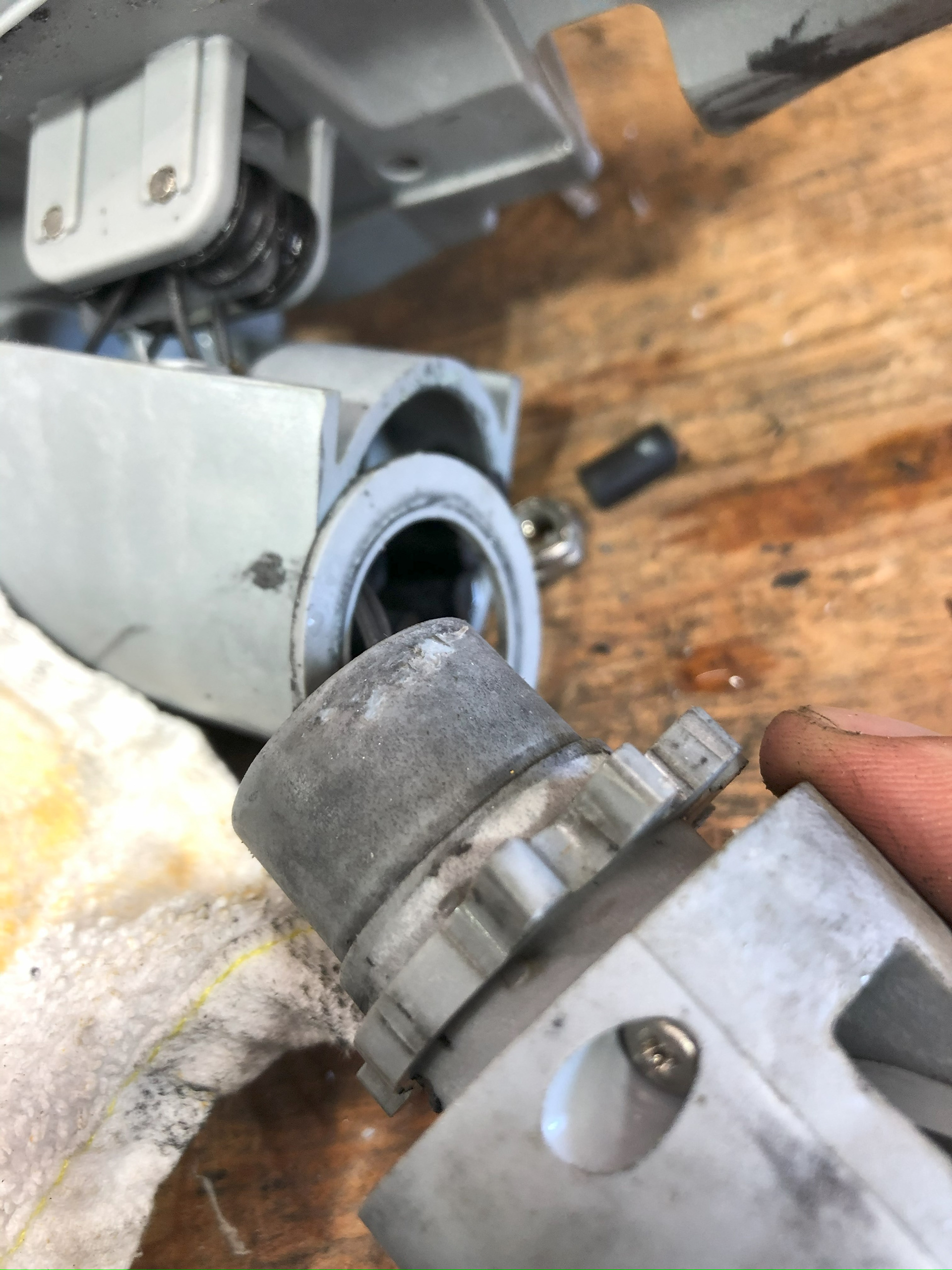
Worn GF bearing surfaces
Pin alignment issue
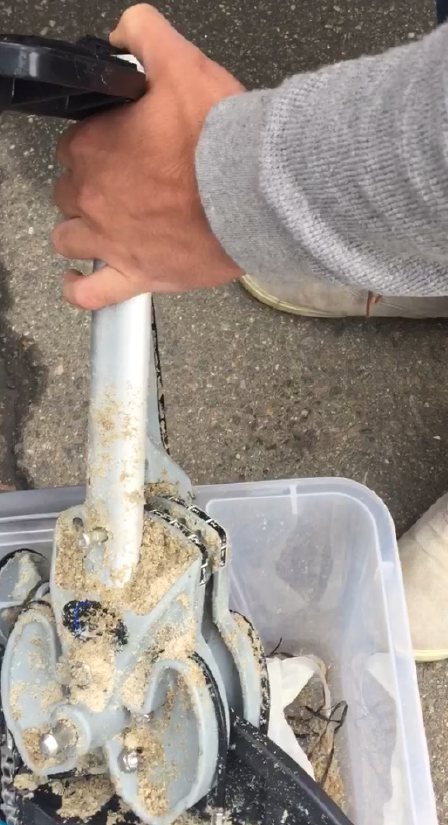
San test cranks
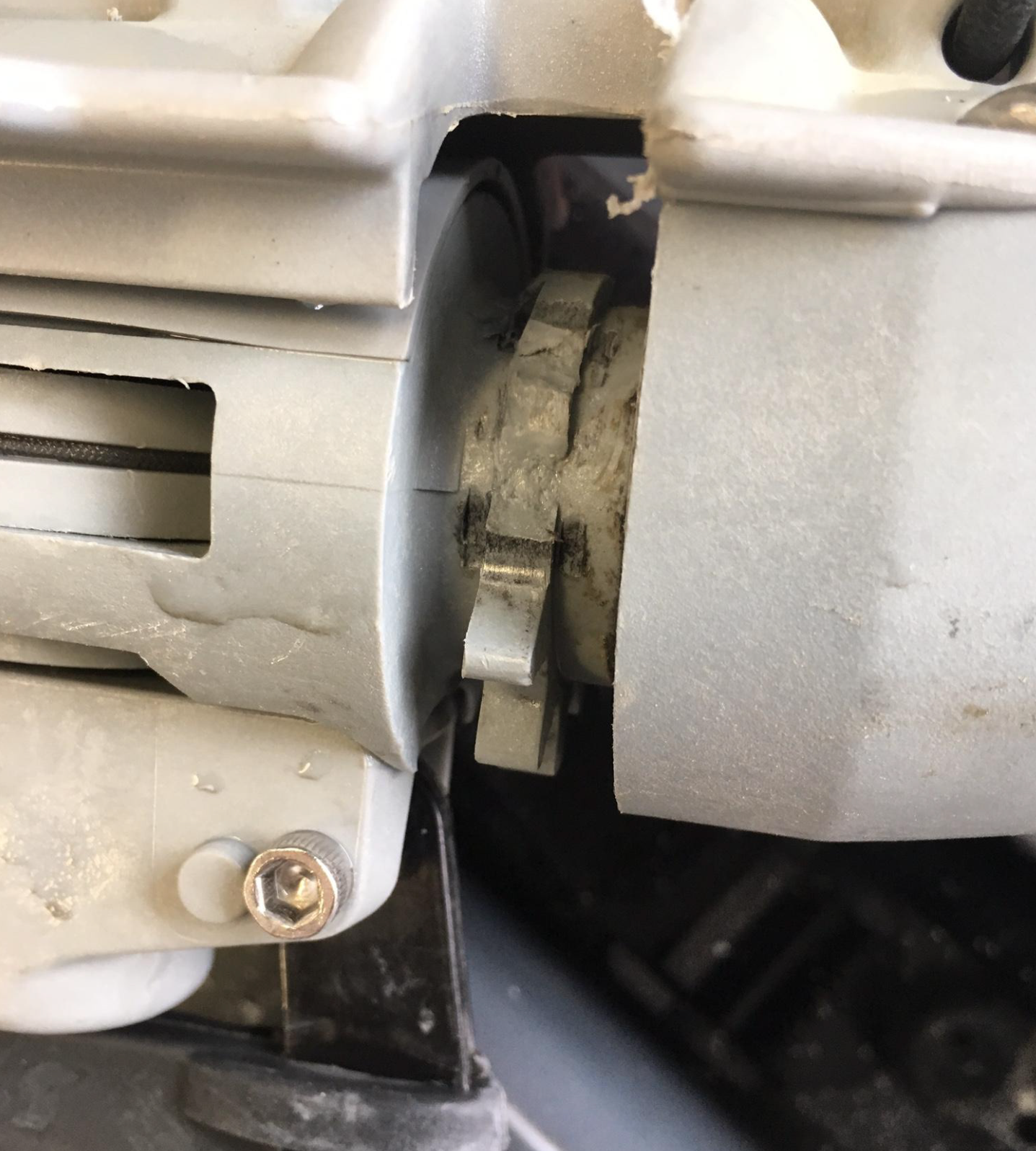
Stripped teeth
Bad Rivet
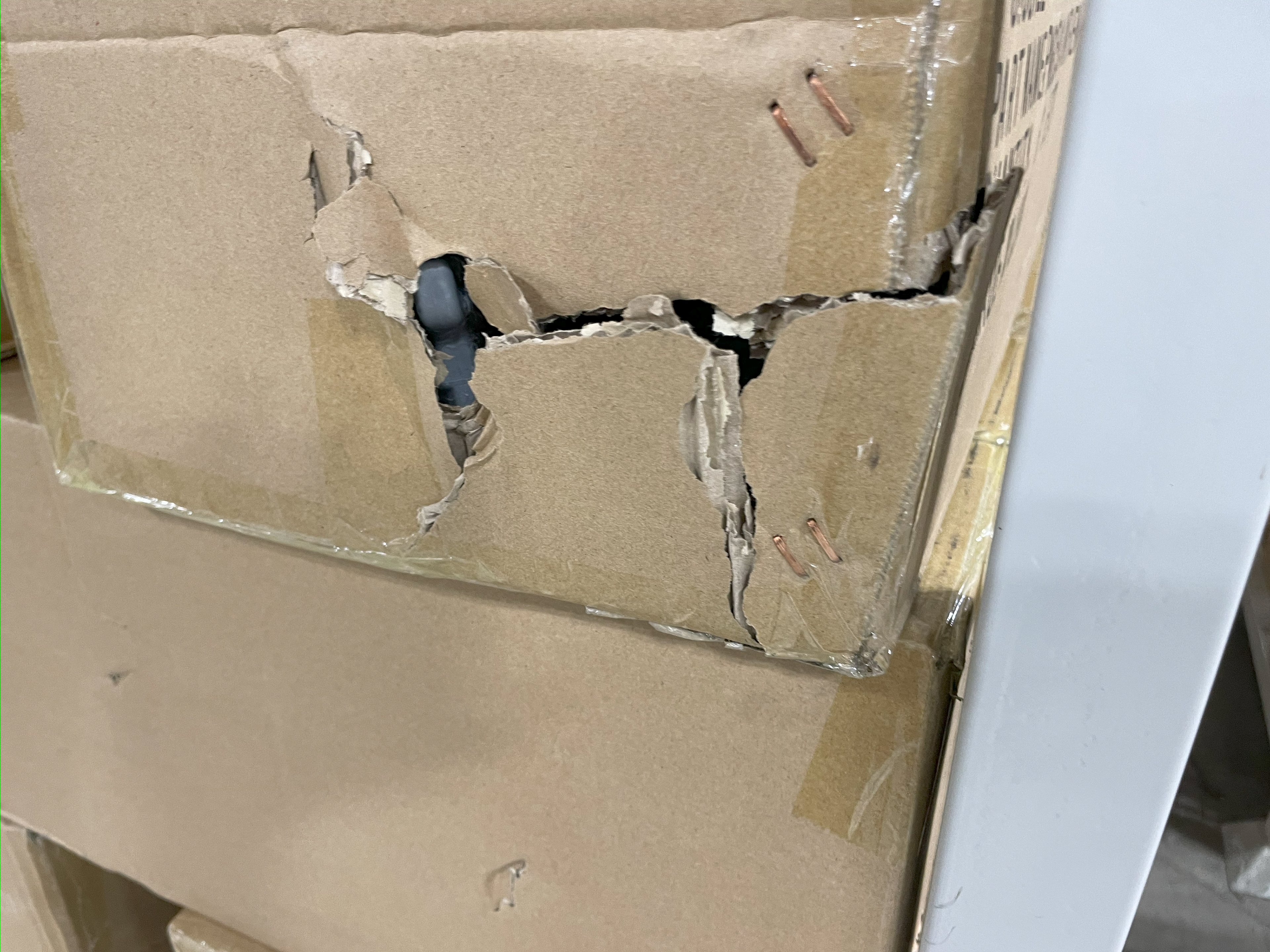
Heavy shipping damage
Fatigue cycle test • UV test • Tensile test • Sand ingress • Saltwater corrosion test • Fin thrust test • Field test
Built to scale
I was responsible for delivering the drives from concept through 80,000 pcs/yr production. Building drives over and over with the assembly team allowed me to improve cycle times, balance the work cells, and decrease error and control quality. I reworked detail drawings, assembly drawings, and QC videos to ensure each assembled drive was built on a feedback loop that helped drive a continuous improvement cycle.
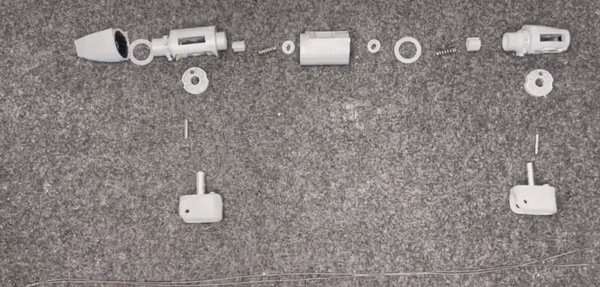
Drive bag samples
detail drawing crank core
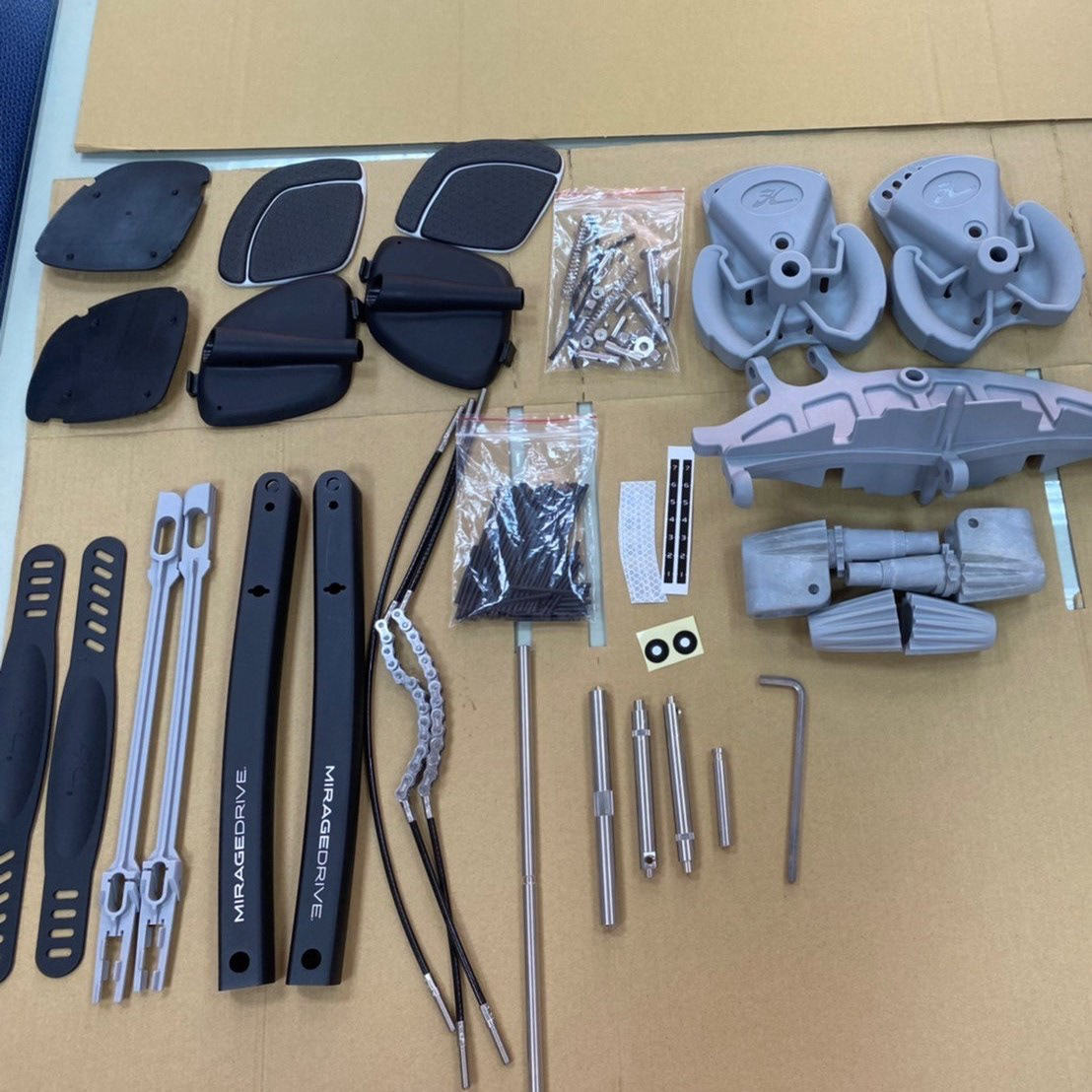
MirageDrive 180 introduction video
MirageDrive 360 introduction video
Design: User needs gathering • Concept design • Prototype development • Patent writing & drawings • A-class surface CAD
Engineering: 60x detail drawings • BOM cost analysis • Vendor quoting • Supply chain management (CHN, TWN, PHL, MEX) • Production QAQC •
Tools: Sketching • Urethane casting • Metal machine shop • SolidWorks • 3D printing • Keyshot
Manufacturing: 55x Injection mold tools • Rotomold hull integration • Alu extrusion/stamp/heat treat/anodize • SS stamp/passivation • CNC machining • Laser etching • Die cutting • Assembly line training • Production fixture design • SS investment casting • LEAN MANUFACTURING
Credit to Phil Dow, inventor of the MirageDrive 360